Determination of steam quantities from a gas-fired boiler plant
Application Report | Power Generation
- Accurate and reliable measuring data for the distribution and calculation of thermal energy
- Calibrated DP flow solutions for flow measurement of HP/LP steam and condensate (acc. to ISO 5167)
- Complete scope of delivery with flow nozzles, orifice meter runs, DP and pressure transmitters, temperature assemblies and flow computers
- Everything supplied from one source: from consultation and engineering to manufacturing and integration
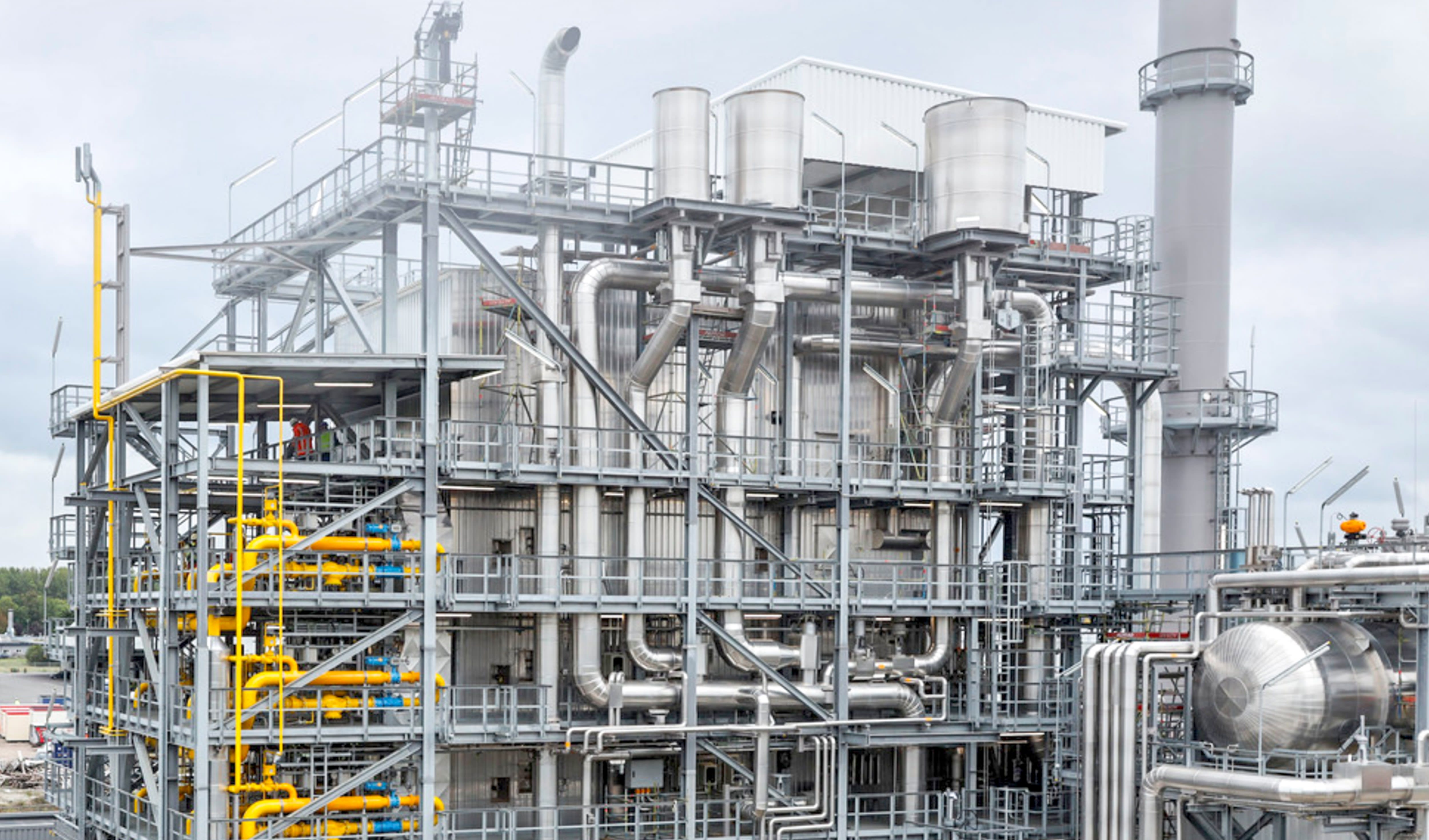
Background
In 2017, international energy supplier E.ON entered into a long-term partnership with Dow Benelux to build, own and operate a large gas-fired boiler plant for their largest production site in Europe, located in Terneuzen, the Netherlands. At the site, Dow is producing chemical intermediates which are further processed for a variety of products in commercial and industrial business such as packaging, coatings and foams.
A new boiler plant was integrated by E.ON Power Plants Belgium into the existing steam distribution grid at the Dow Benelux site in Terneuzen. The boiler has dual-fuel capabilities and can be operated on all mixtures of natural gas, hydrogen of up to 45% and the by-product fuel gas of the naphtha crackers. The boiler plant and the necessary components were designed for extreme requirements of load gradients, steam pressure tolerance and availability.
Measurement requirements
In order to be able to distribute and determine the produced steam quantities as well as to measure the return flow of polished condensate, the plant had to be equipped with suitable measuring technology. This must be capable to measure with high accuracy over a large dynamic measuring range. For heat and mass balancing, the energy supplier required the measurement technology to be highly accurate in service, long-term stable and in accordance with the ISO 5167 standard. This implied that all meter runs need to be traceably calibrated at high Reynolds numbers.
KROHNE Solution
Having considered different approaches to steam measurement, the plant operator decided in favour of KROHNE’s differential pressure (DP) solution with an ISA 1932 nozzle as it was the most efficient choice when it comes to accuracy and long-term stability. The DP flow measurement with nozzle was engineered in accordance with ISO 5167 and ASME MFC-3M standards as per customer requirement. The KROHNE scope of delivery for high-pressure (HP) steam, low-pressure (LP) steam and polished condensate measurement included six calibrated ISA 1932 nozzles (3 for HP steam, 3 for LP steam) and three calibrated OPTIBAR MR 4300 orifice meter runs (for condensate). The primary flow elements were installed in combination with the OPTIBAR DP 7060 differential pressure transmitter (incl. 5-way manifolds), the OPTITEMP TRA-S34 temperature assembly (incl. OPTITEMP TT 33 R rail-mounted temperature transmitter), plus the OPTIBAR PM 5060 pressure transmitter (with 3-way manifolds). As energy management in this project requires dedicated flow computing to determine the quantity and financial value of the HP/LP steam export as well as the import of polished condensate, KROHNE also provided a flow computer that calculates the energy of steam and condensate from the input variables flow rate, (differential) pressure and temperature.
Customer benefits
Using KROHNE’s integrated DP flow solutions, the operator benefits from reliable and accurate data for heat and mass balancing. Given that even a small error can amount to a large financial difference in those projects, the calibrated DP flow solutions turned out to offer the best OPEX for the operator as they are long-term stable and accurate over a wide dynamic range. Designed in accordance with ISO 5167, the measured values of the DP flowmeters can be checked for plausibility during process operation, thus ensuring that the measuring devices still work accurately and reliably as per customer specification. KROHNE as a main instrument vendor (MIV) for this solution provided the whole scope of delivery - from consulting, engineering, manufacturing and testing to project management and integration of the measuring equipment into the operator's process control system.