Storage in prepared pet food production
Handling of meat mixtures with other ingredients such as cereal grains, vitamins and minerals
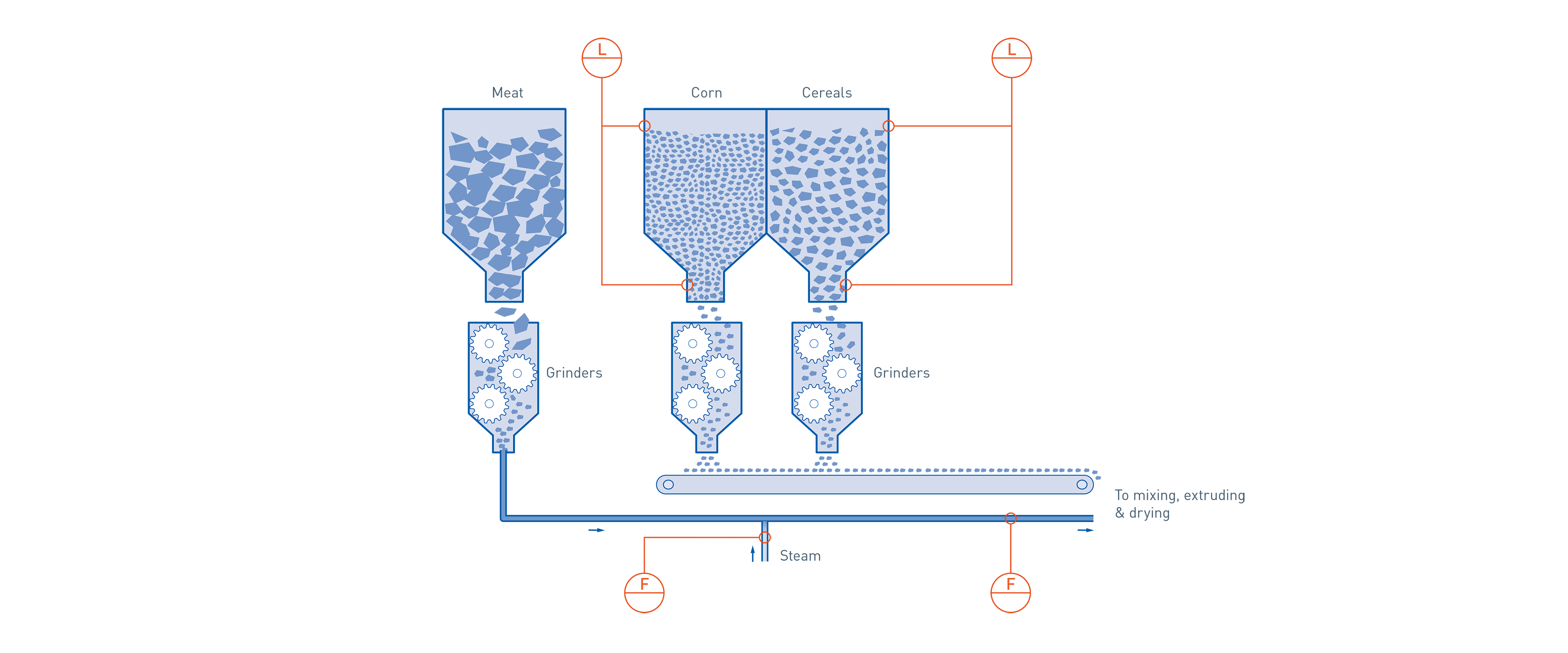
The products used are fed from hoppers, and coarsely ground to the desired texture. To facilitate further processing, the ground meat is cooked in a continuous cooker with live steam at an appropriate temperature. The meat mixture is then blended with other ingredients such as cereal grains, vitamins, and minerals, from their respective hoppers/grinders or storage vessels, and carefully delivered together in the correct proportions for mixing and packing. Dry and semi-moist foods are usually heated so that the mixture will partially thicken the starch present (‘dextrinisation’).
Level control in the hoppers is achieved with OPTISWITCH capacitive probes, to provide high and low alarms even in relatively dry materials. The flow of live steam to cook the meat can be measured and controlled with the OPTISWIRL vortex flowmeter. The OPTIMASS Coriolis mass flowmeter finally measures and signals the mass flow rate of the cooked meat into the mixing tank. Based on the improved functionality of the OPTIMASS Coriolis meters by KROHNE, it is possible to switch from the conventional batch processes to continuous inline processes. Even high viscous products like grinded meat can be measured inline by OPTIMASS Coriolis flowmeters.
Process details
Storage in prepared pet food production
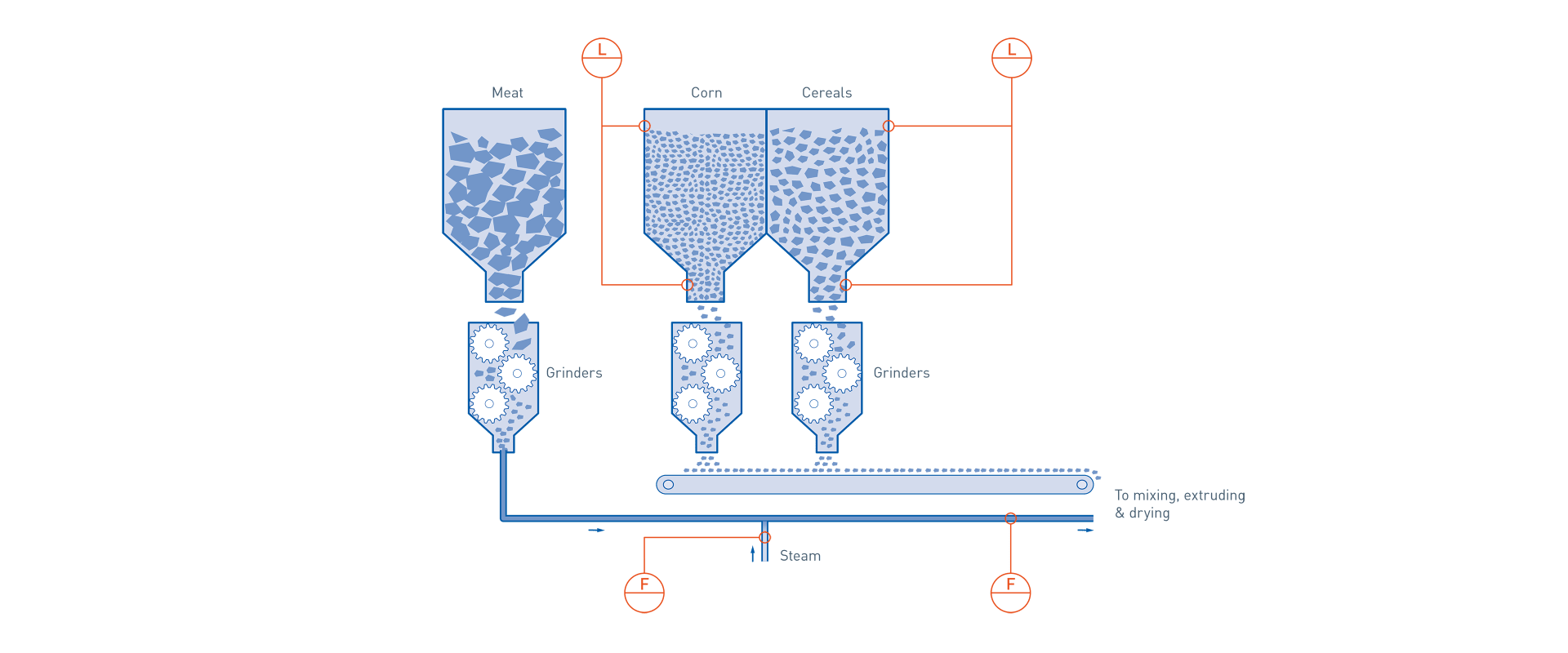
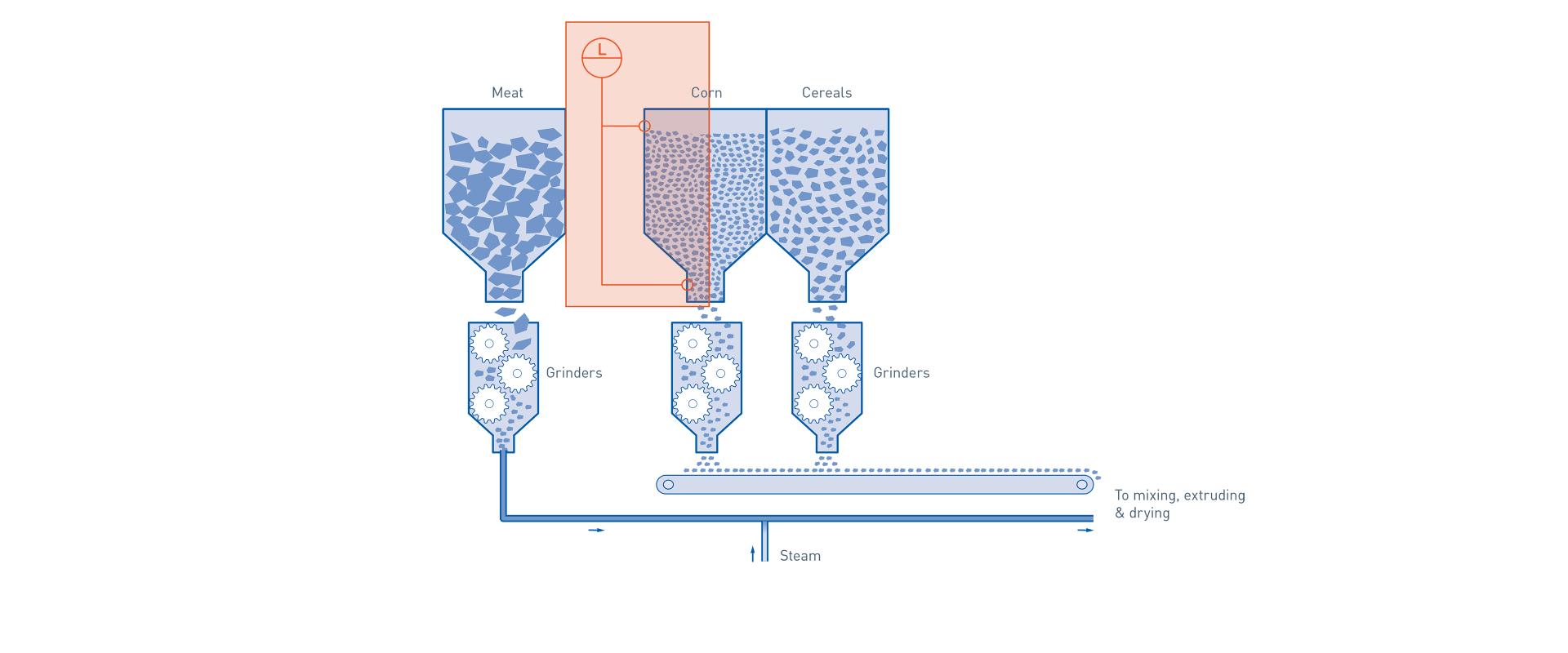
Requirements:
- Handling of dusty atmosphere
- High shear forces
Recommended products and solutions:
OPTISWITCH 6600
- Point level detection of solids, liquids and liquid-liquid interface
- Wide variety of hygienic process connections available
- -20…+200°C / -4…+392°F; -1…16 barg / -14.5…580 psig
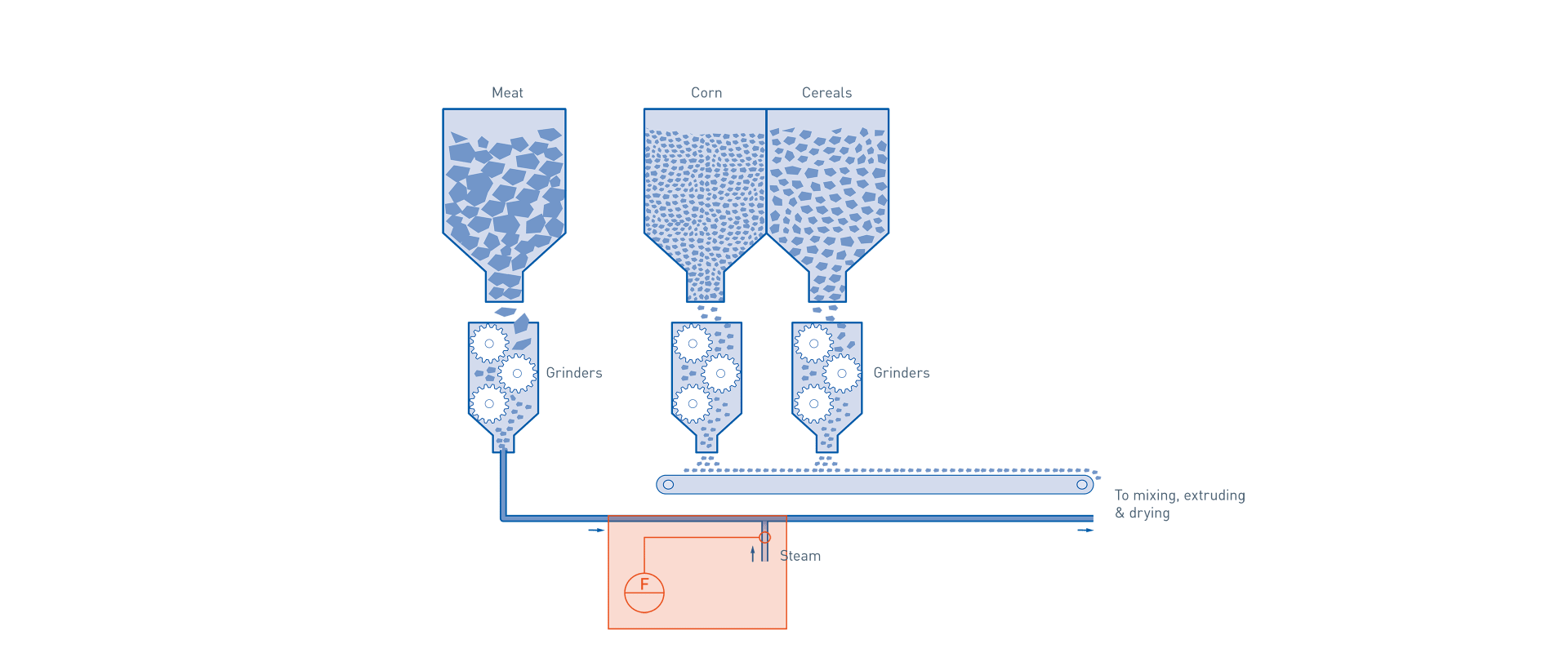
Requirements:
- Pressure/ temperature compensated
- Net heat measurement
Recommended products and solutions:
OPTISWIRL 4200
- For liquids, (wet) gases, saturated and superheated steam (+240°C / +464°F)
- Integrated P+T measurement: direct output of mass, nominal flow, energy, gross/net heat
- Flange: DN15…300 / ½…12"; wafer version: max. DN100 / 4"
- 2-wire, 4…20 mA, HART®, FF, Profibus-PA
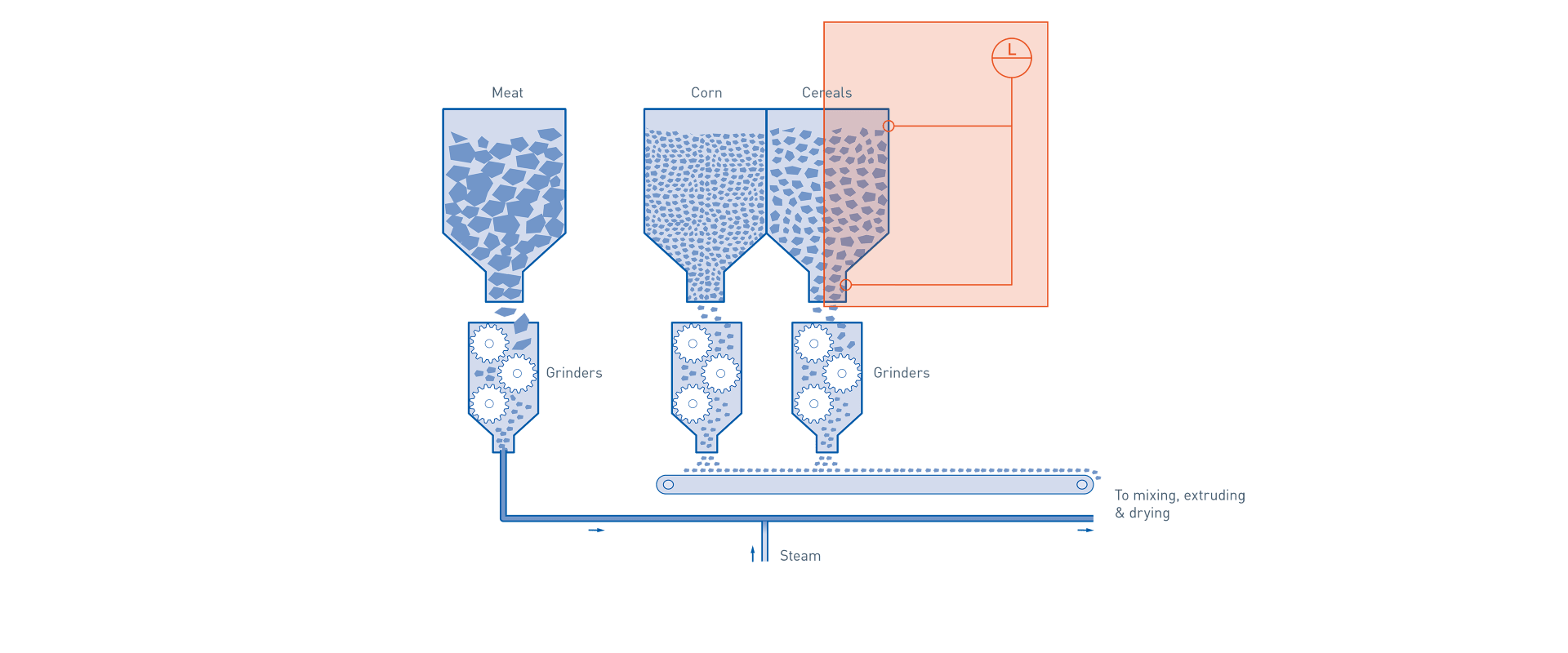
Requirements:
- Handling of dusty atmosphere
- High shear forces
Recommended products and solutions:
OPTISWITCH 6600
- Point level detection of solids, liquids and liquid-liquid interface
- Wide variety of hygienic process connections available
- -20…+200°C / -4…+392°F; -1…16 barg / -14.5…580 psig
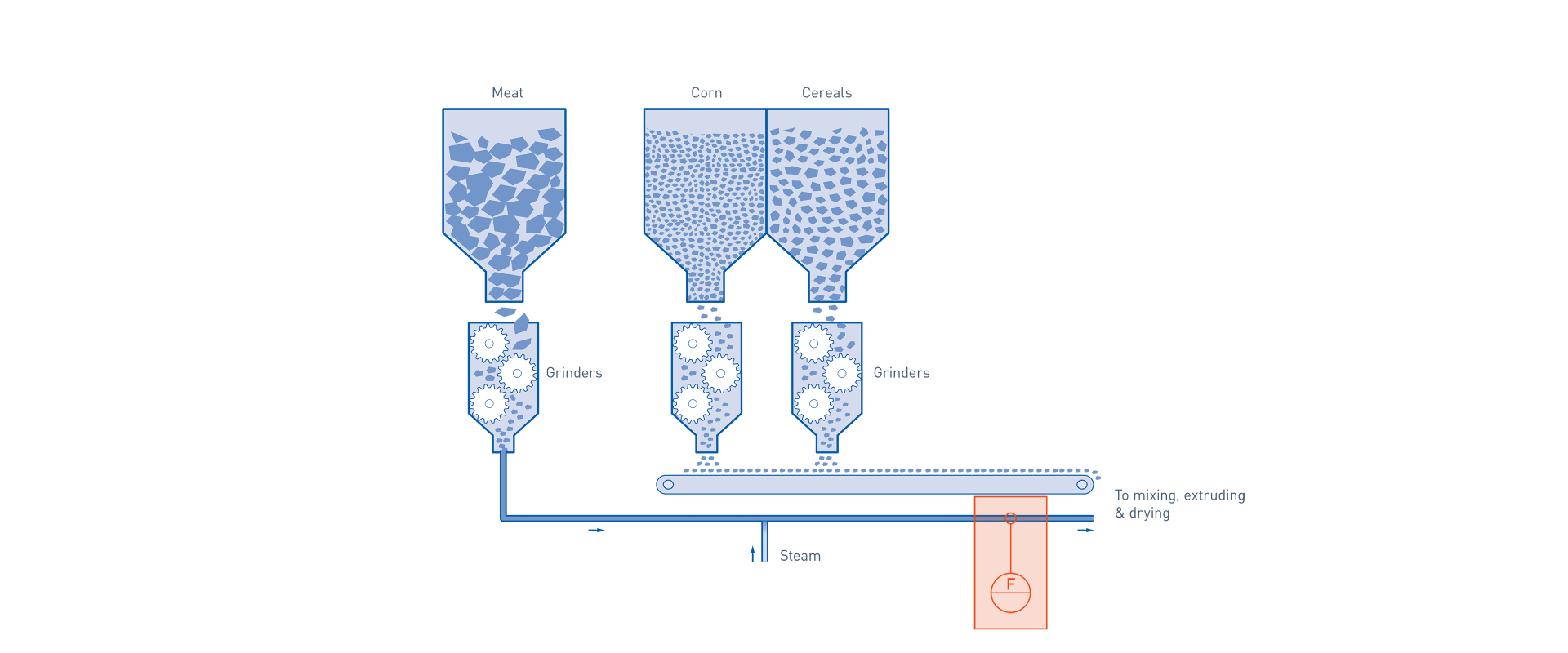
Requirements:
- Handling of very viscous media and high density
- Handling of air entrainment
Recommended products and solutions:
OPTIMASS 7400
- High accuracy (±0.1%), for viscous, aggressive or shear-sensitive media; maintains operation over a wide range of gas fractions and complex flow conditions (EGMTM)
- CT: OIML R117, MI-005; API; hygienic certifications
- Flange: DN10…100 / ½…4", max. PN100 / ASME Cl 600; others
- 3 x 4…20 mA, HART®7, Modbus, FF, Profibus-PA/DP, PROFINET, EtherNet/IP™, Bluetooth®
Storage in prepared pet food production
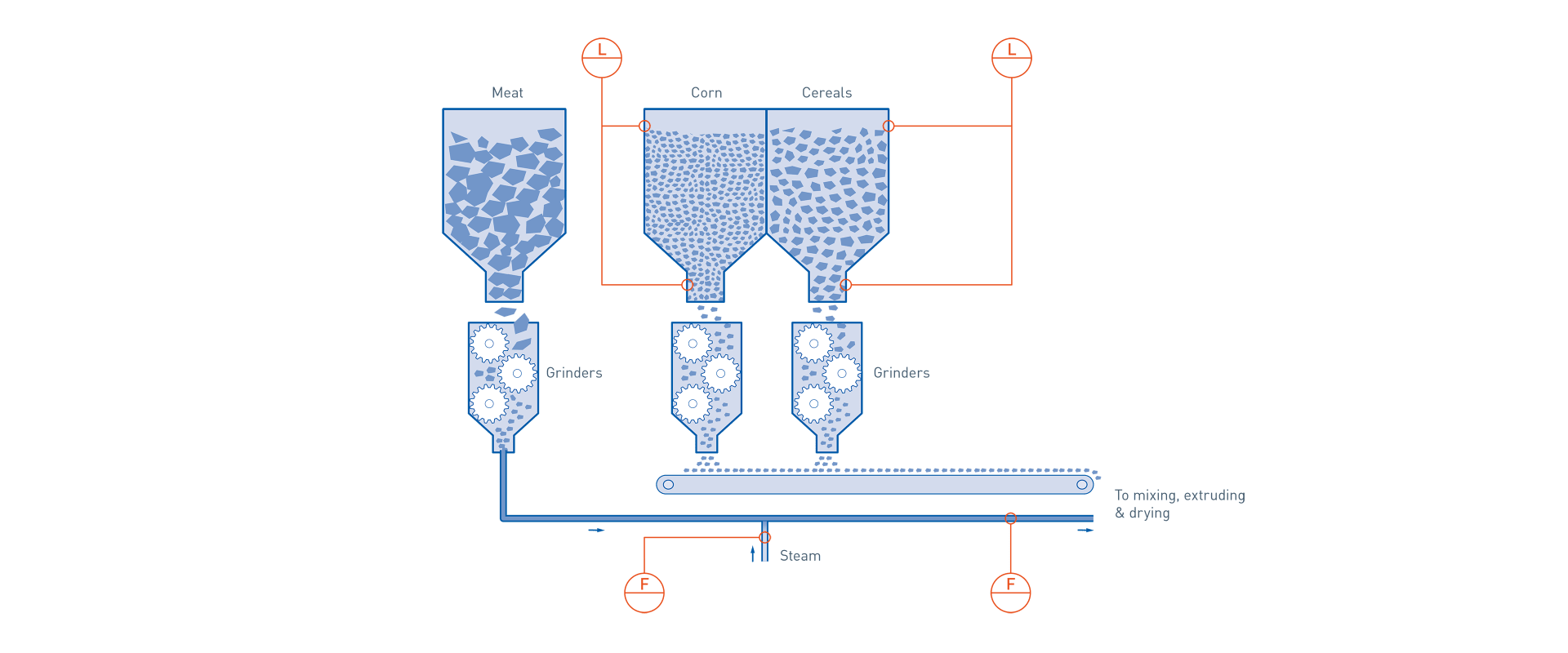
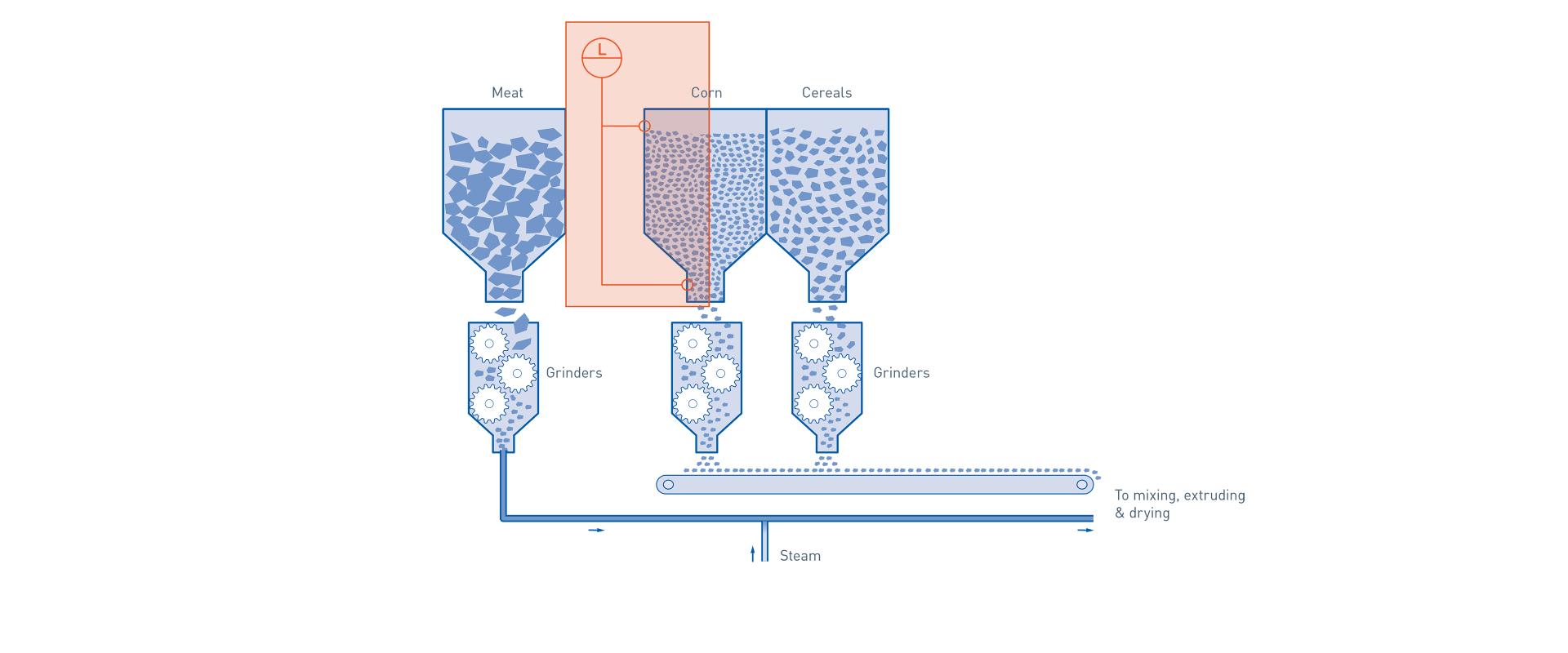
Requirements:
- Handling of dusty atmosphere
- High shear forces
Recommended products and solutions:
OPTISWITCH 6600
- Point level detection of solids, liquids and liquid-liquid interface
- Wide variety of hygienic process connections available
- -20…+200°C / -4…+392°F; -1…16 barg / -14.5…580 psig
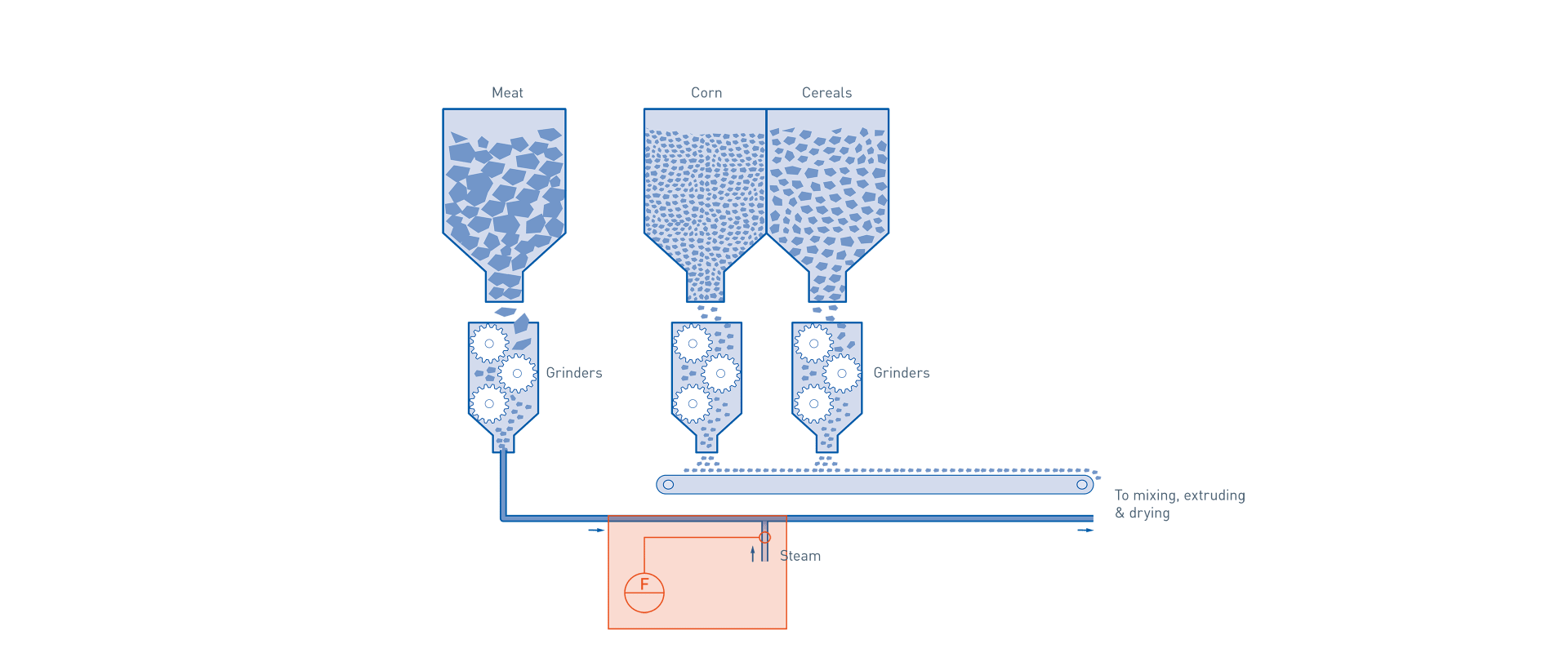
Requirements:
- Pressure/ temperature compensated
- Net heat measurement
Recommended products and solutions:
OPTISWIRL 4200
- For liquids, (wet) gases, saturated and superheated steam (+240°C / +464°F)
- Integrated P+T measurement: direct output of mass, nominal flow, energy, gross/net heat
- Flange: DN15…300 / ½…12"; wafer version: max. DN100 / 4"
- 2-wire, 4…20 mA, HART®, FF, Profibus-PA
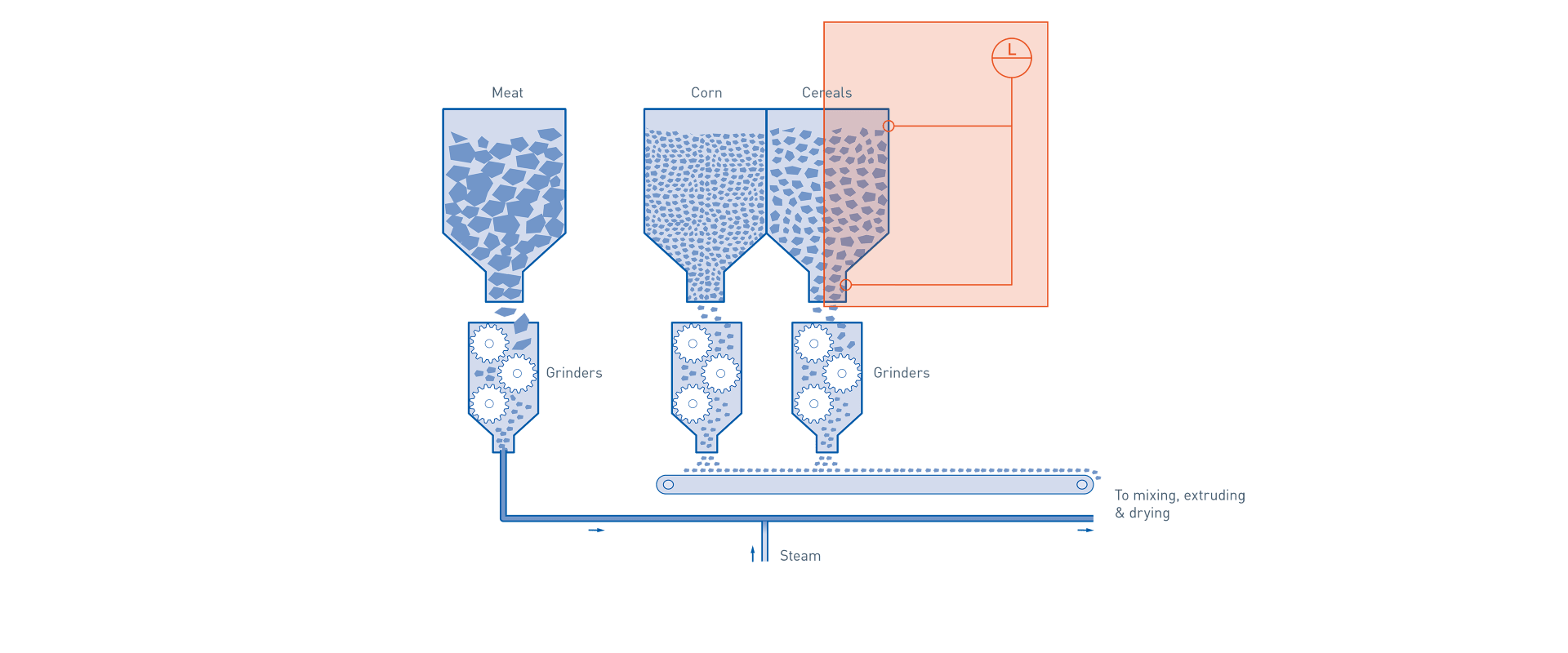
Requirements:
- Handling of dusty atmosphere
- High shear forces
Recommended products and solutions:
OPTISWITCH 6600
- Point level detection of solids, liquids and liquid-liquid interface
- Wide variety of hygienic process connections available
- -20…+200°C / -4…+392°F; -1…16 barg / -14.5…580 psig
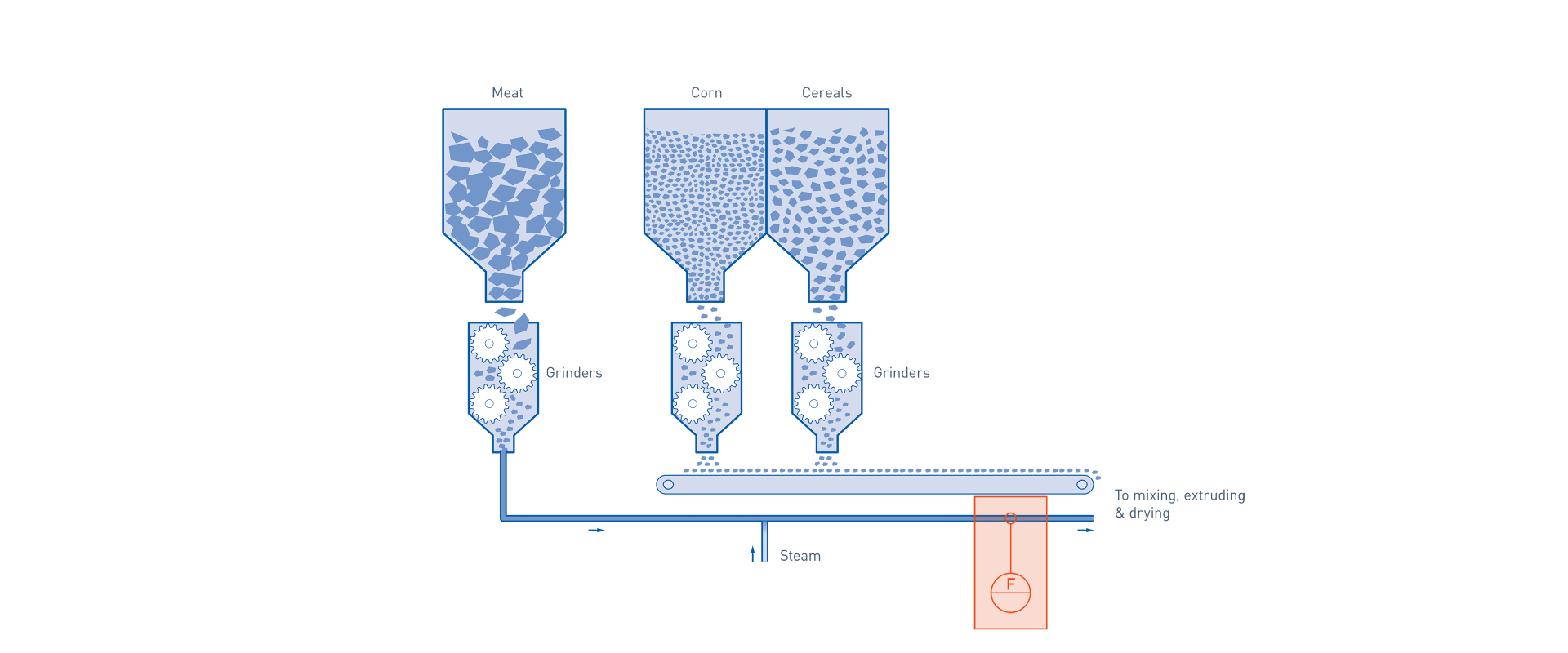
Requirements:
- Handling of very viscous media and high density
- Handling of air entrainment
Recommended products and solutions:
OPTIMASS 7400
- High accuracy (±0.1%), for viscous, aggressive or shear-sensitive media; maintains operation over a wide range of gas fractions and complex flow conditions (EGMTM)
- CT: OIML R117, MI-005; API; hygienic certifications
- Flange: DN10…100 / ½…4", max. PN100 / ASME Cl 600; others
- 3 x 4…20 mA, HART®7, Modbus, FF, Profibus-PA/DP, PROFINET, EtherNet/IP™, Bluetooth®
Requirements:
- Handling of dusty atmosphere
- High shear forces
Recommended products and solutions:
OPTISWITCH 6600
Capacitance level switch for hygienic and industrial applications
Storage in prepared pet food production
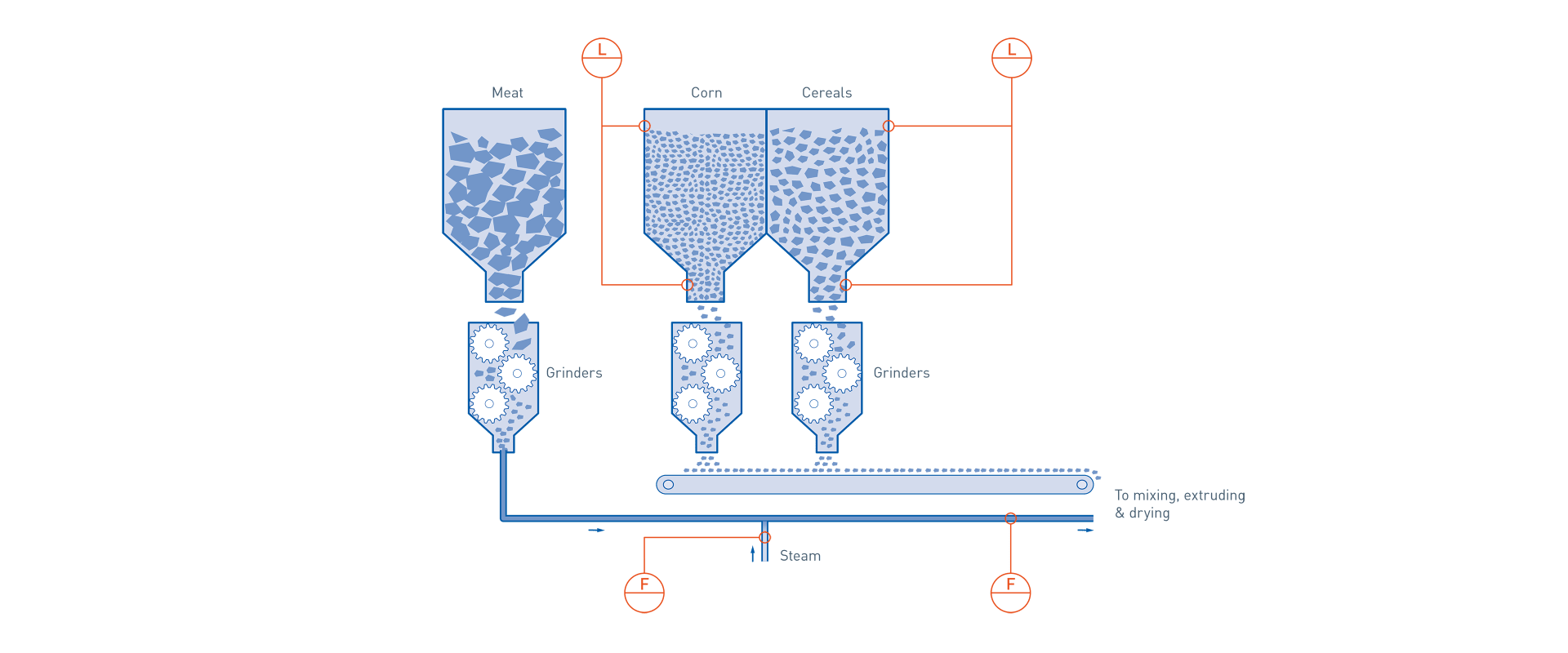
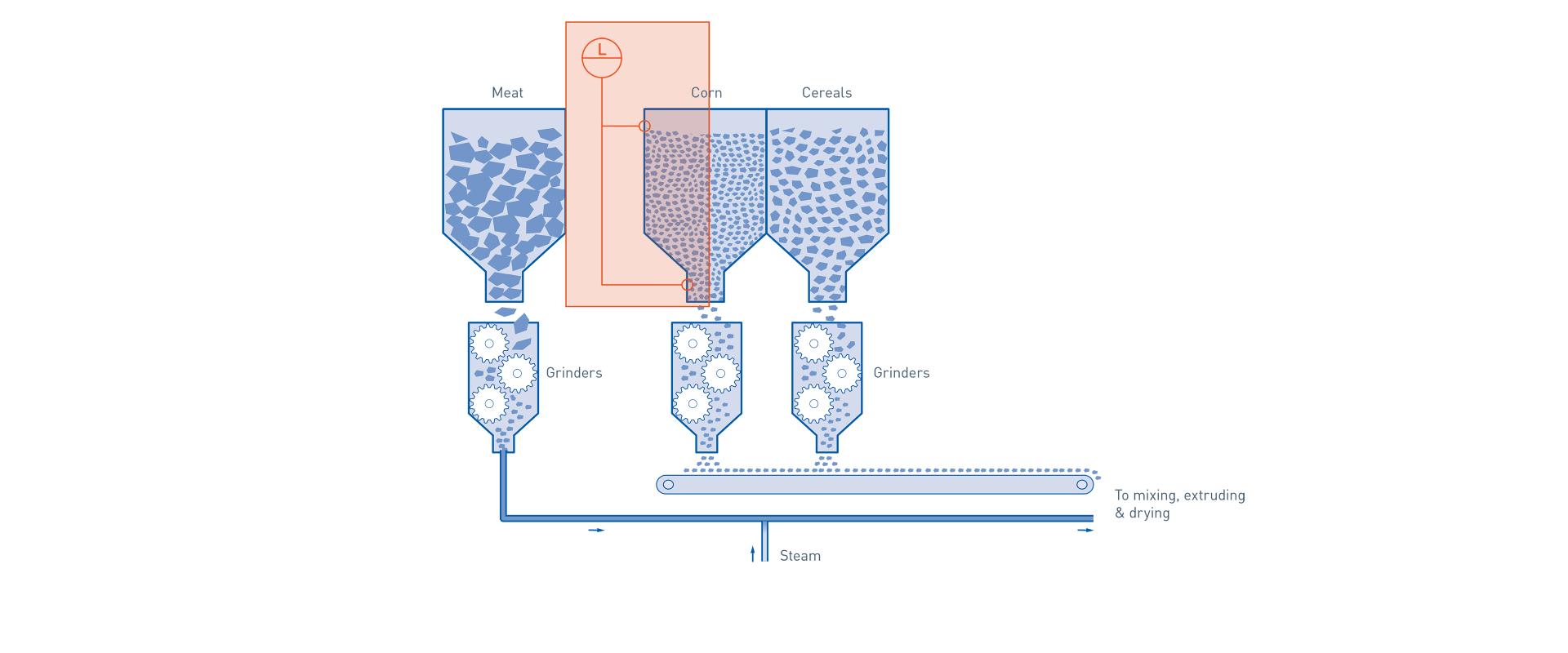
Requirements:
- Handling of dusty atmosphere
- High shear forces
Recommended products and solutions:
OPTISWITCH 6600
- Point level detection of solids, liquids and liquid-liquid interface
- Wide variety of hygienic process connections available
- -20…+200°C / -4…+392°F; -1…16 barg / -14.5…580 psig
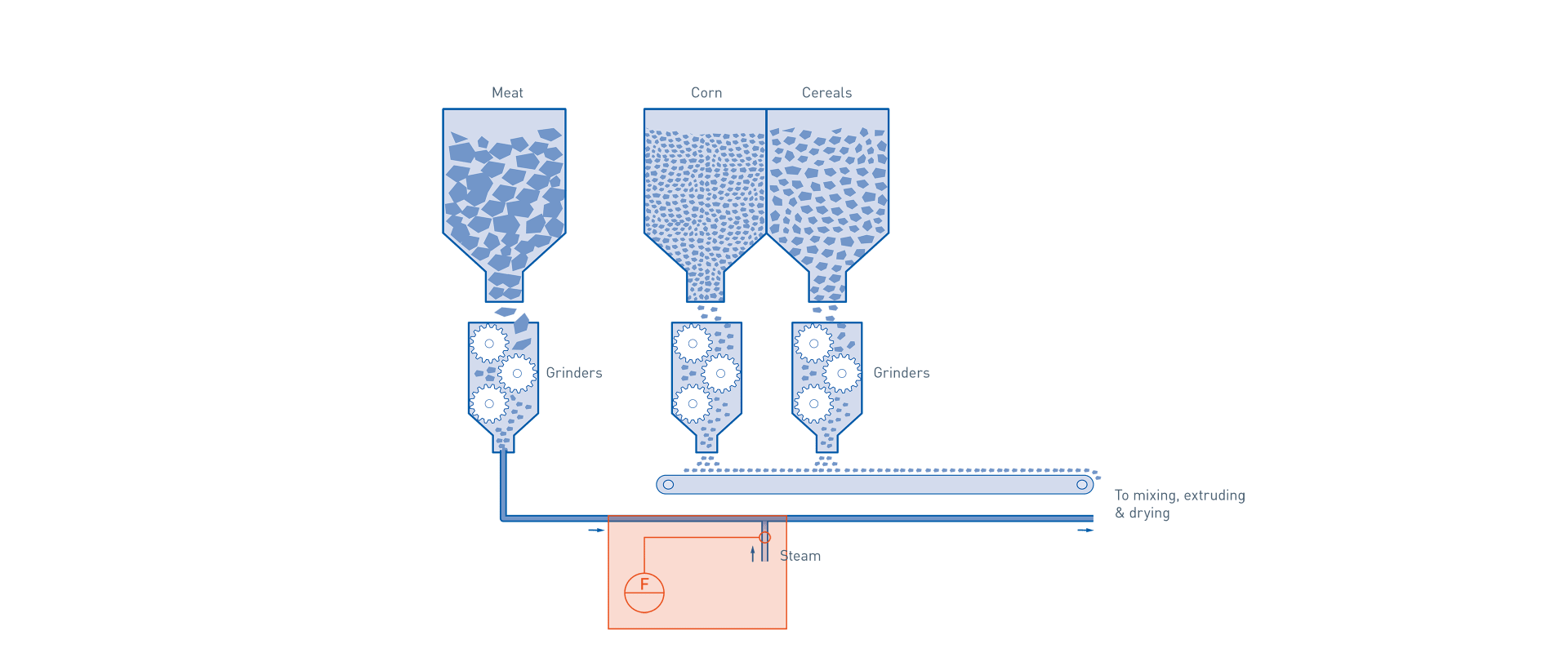
Requirements:
- Pressure/ temperature compensated
- Net heat measurement
Recommended products and solutions:
OPTISWIRL 4200
- For liquids, (wet) gases, saturated and superheated steam (+240°C / +464°F)
- Integrated P+T measurement: direct output of mass, nominal flow, energy, gross/net heat
- Flange: DN15…300 / ½…12"; wafer version: max. DN100 / 4"
- 2-wire, 4…20 mA, HART®, FF, Profibus-PA
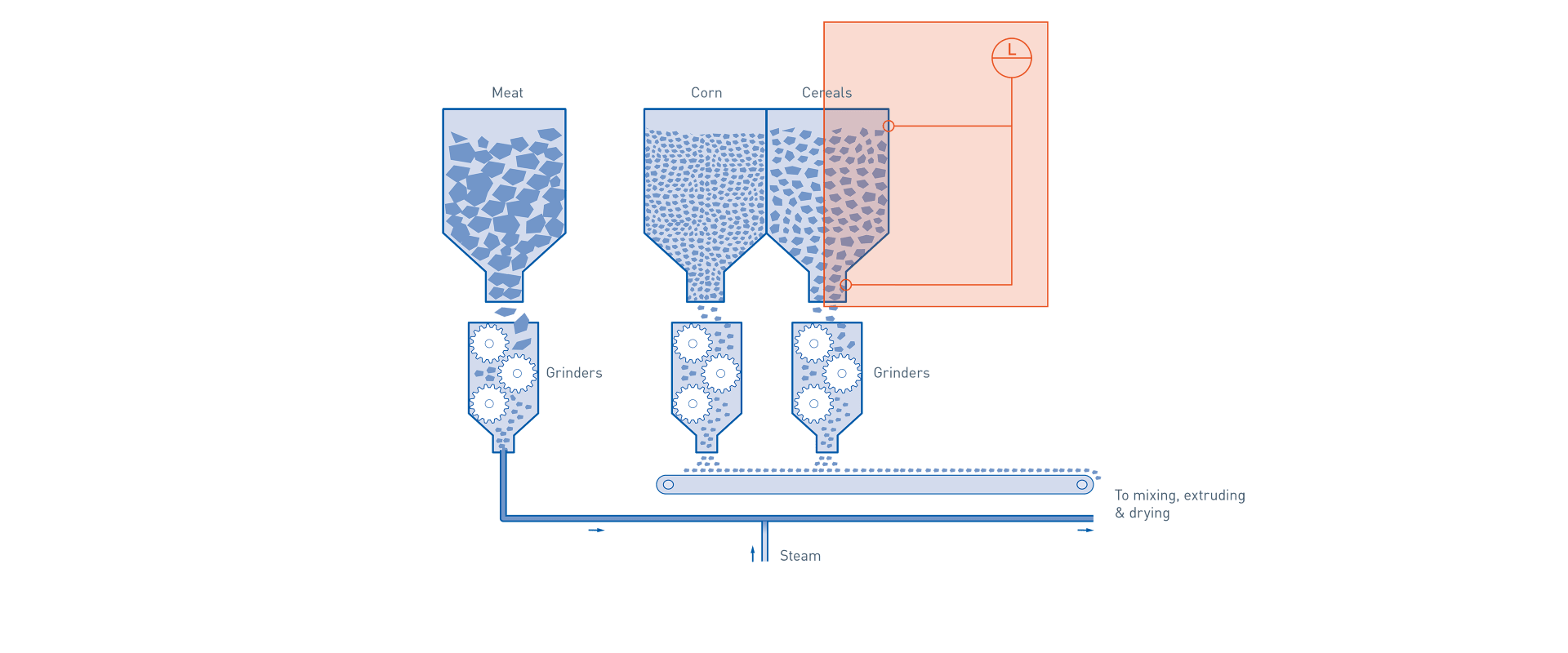
Requirements:
- Handling of dusty atmosphere
- High shear forces
Recommended products and solutions:
OPTISWITCH 6600
- Point level detection of solids, liquids and liquid-liquid interface
- Wide variety of hygienic process connections available
- -20…+200°C / -4…+392°F; -1…16 barg / -14.5…580 psig
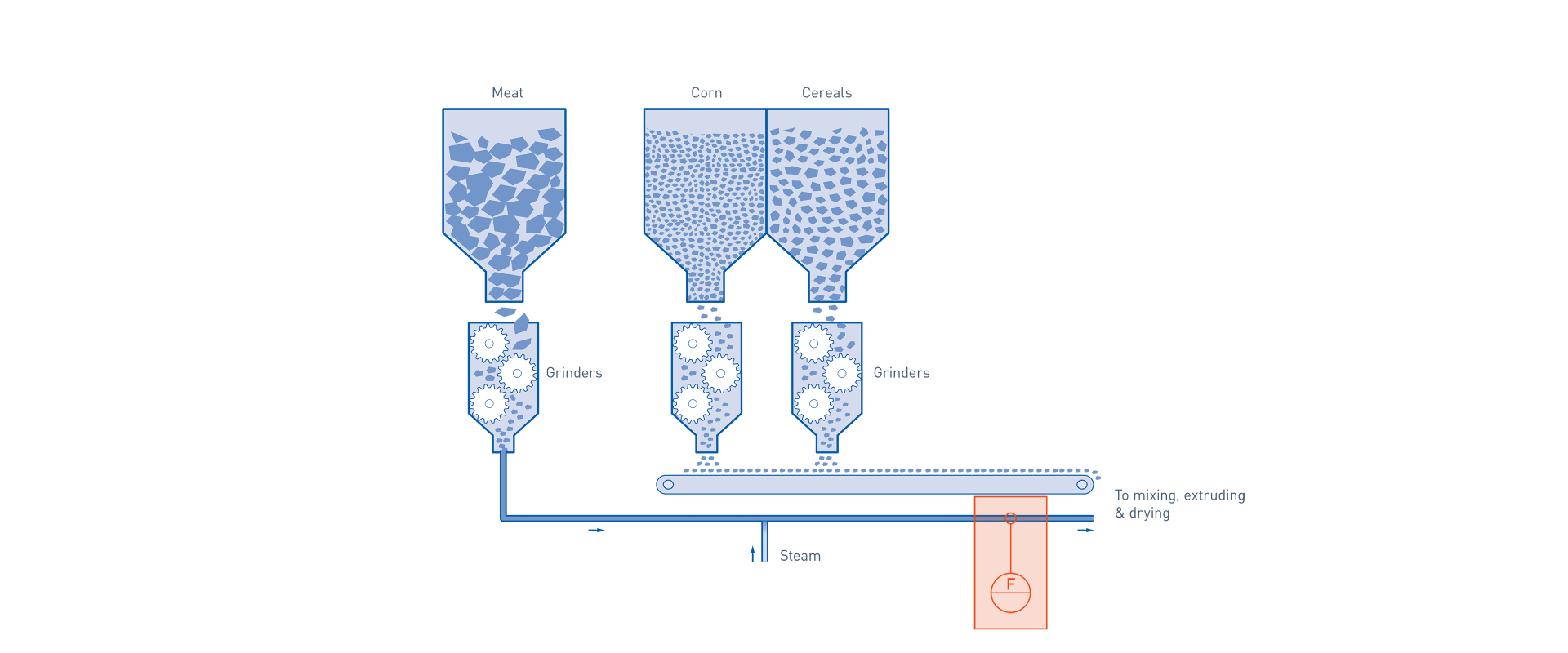
Requirements:
- Handling of very viscous media and high density
- Handling of air entrainment
Recommended products and solutions:
OPTIMASS 7400
- High accuracy (±0.1%), for viscous, aggressive or shear-sensitive media; maintains operation over a wide range of gas fractions and complex flow conditions (EGMTM)
- CT: OIML R117, MI-005; API; hygienic certifications
- Flange: DN10…100 / ½…4", max. PN100 / ASME Cl 600; others
- 3 x 4…20 mA, HART®7, Modbus, FF, Profibus-PA/DP, PROFINET, EtherNet/IP™, Bluetooth®
Requirements:
- Pressure/ temperature compensated
- Net heat measurement
Recommended products and solutions:
OPTISWIRL 4200
Vortex flowmeter for utility applications and energy management systems
Storage in prepared pet food production
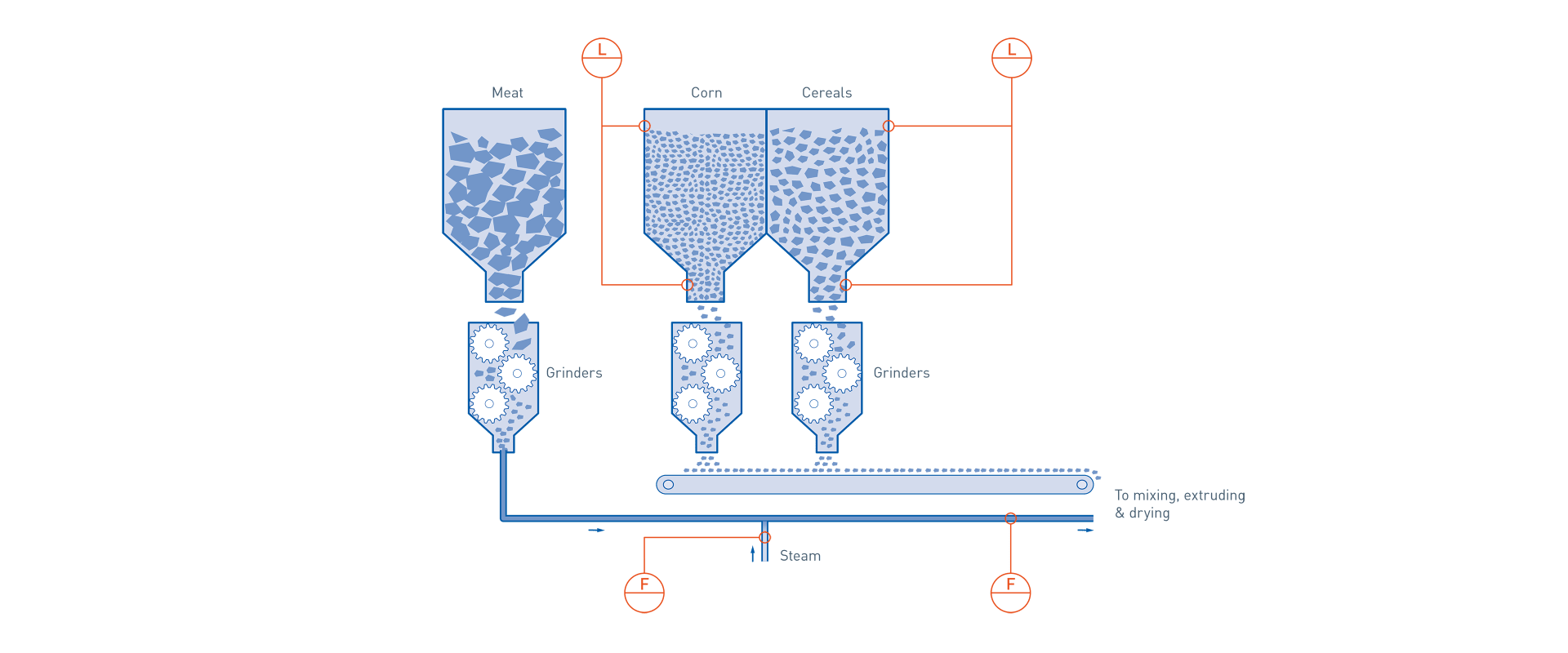
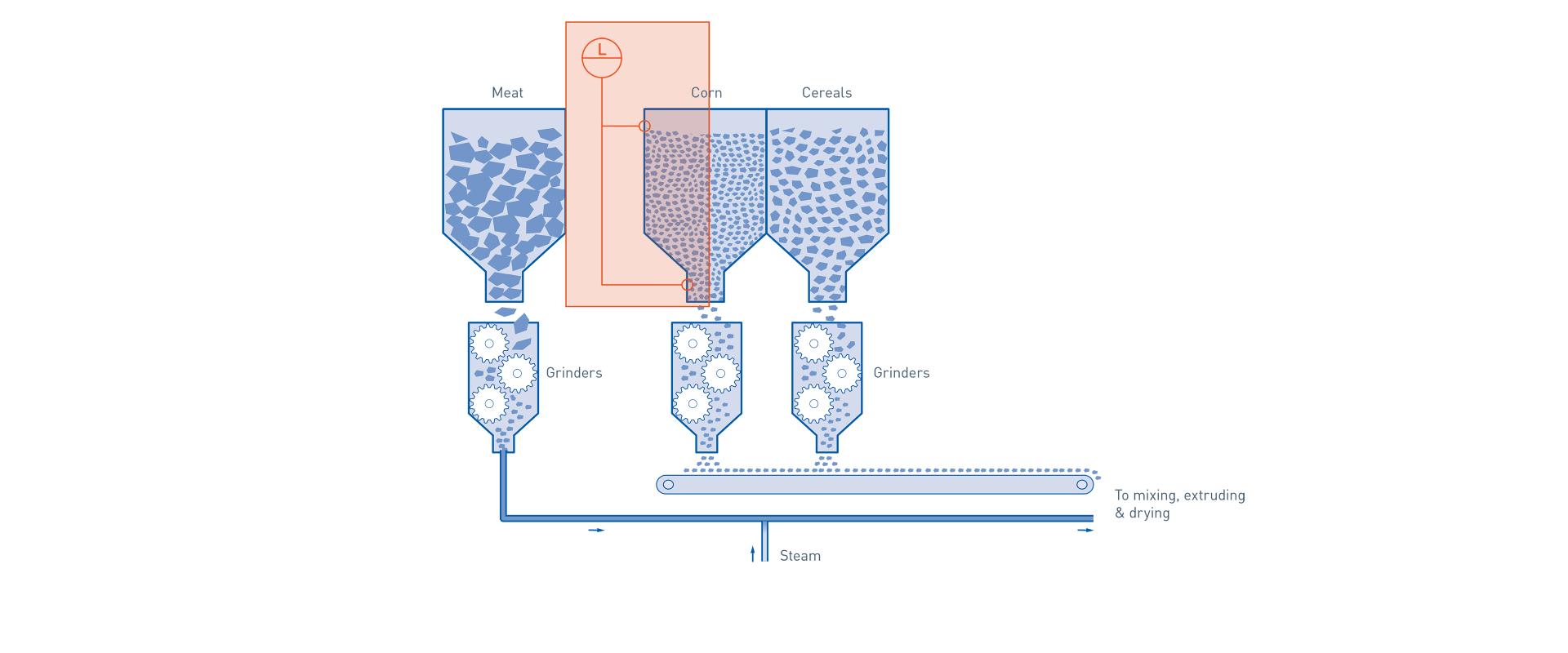
Requirements:
- Handling of dusty atmosphere
- High shear forces
Recommended products and solutions:
OPTISWITCH 6600
- Point level detection of solids, liquids and liquid-liquid interface
- Wide variety of hygienic process connections available
- -20…+200°C / -4…+392°F; -1…16 barg / -14.5…580 psig
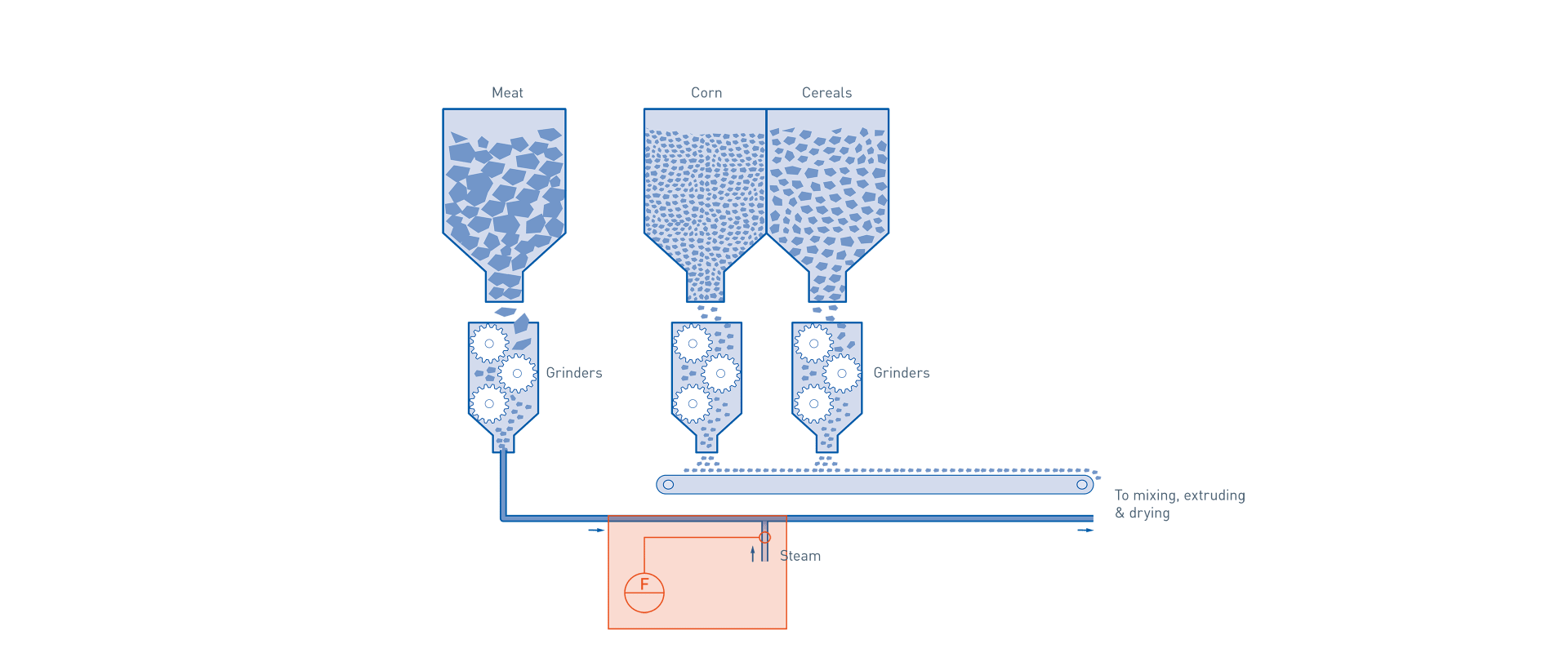
Requirements:
- Pressure/ temperature compensated
- Net heat measurement
Recommended products and solutions:
OPTISWIRL 4200
- For liquids, (wet) gases, saturated and superheated steam (+240°C / +464°F)
- Integrated P+T measurement: direct output of mass, nominal flow, energy, gross/net heat
- Flange: DN15…300 / ½…12"; wafer version: max. DN100 / 4"
- 2-wire, 4…20 mA, HART®, FF, Profibus-PA
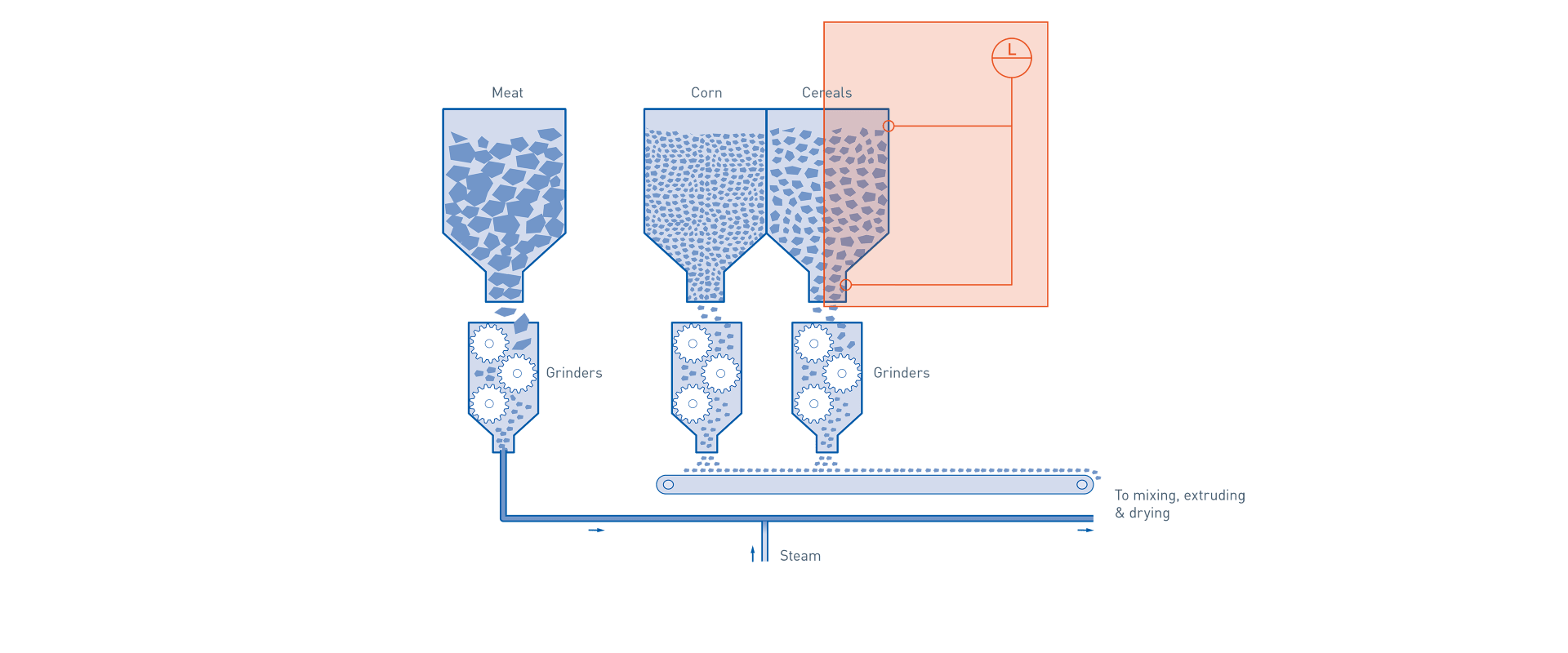
Requirements:
- Handling of dusty atmosphere
- High shear forces
Recommended products and solutions:
OPTISWITCH 6600
- Point level detection of solids, liquids and liquid-liquid interface
- Wide variety of hygienic process connections available
- -20…+200°C / -4…+392°F; -1…16 barg / -14.5…580 psig
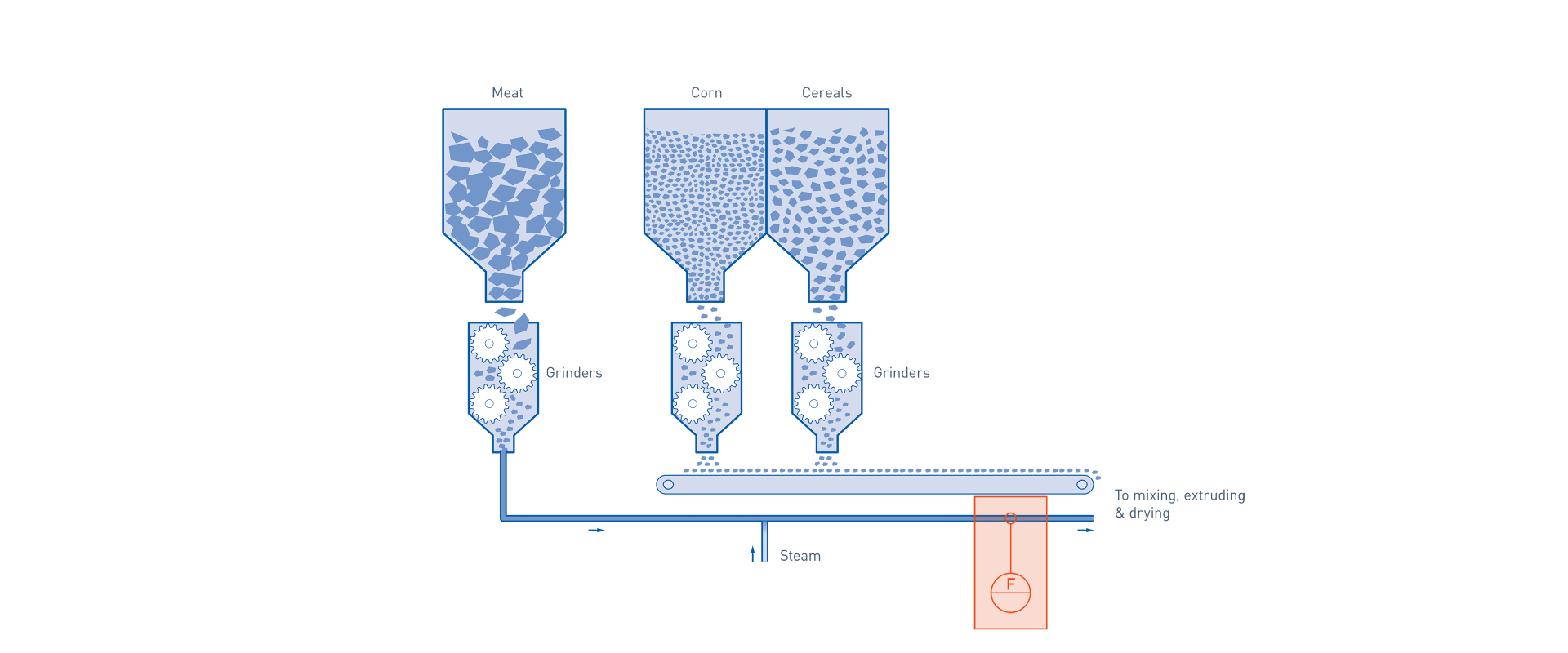
Requirements:
- Handling of very viscous media and high density
- Handling of air entrainment
Recommended products and solutions:
OPTIMASS 7400
- High accuracy (±0.1%), for viscous, aggressive or shear-sensitive media; maintains operation over a wide range of gas fractions and complex flow conditions (EGMTM)
- CT: OIML R117, MI-005; API; hygienic certifications
- Flange: DN10…100 / ½…4", max. PN100 / ASME Cl 600; others
- 3 x 4…20 mA, HART®7, Modbus, FF, Profibus-PA/DP, PROFINET, EtherNet/IP™, Bluetooth®
Requirements:
- Handling of dusty atmosphere
- High shear forces
Recommended products and solutions:
OPTISWITCH 6600
Capacitance level switch for hygienic and industrial applications
Storage in prepared pet food production
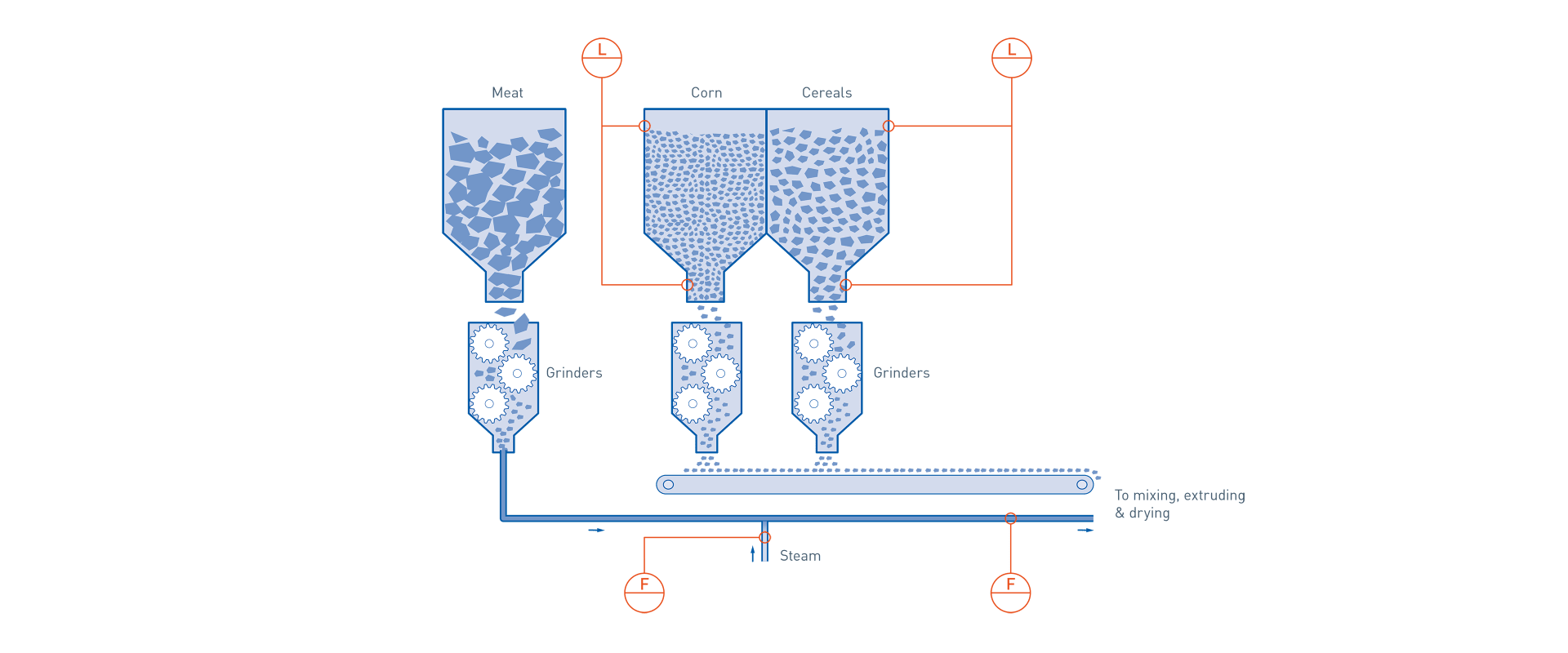
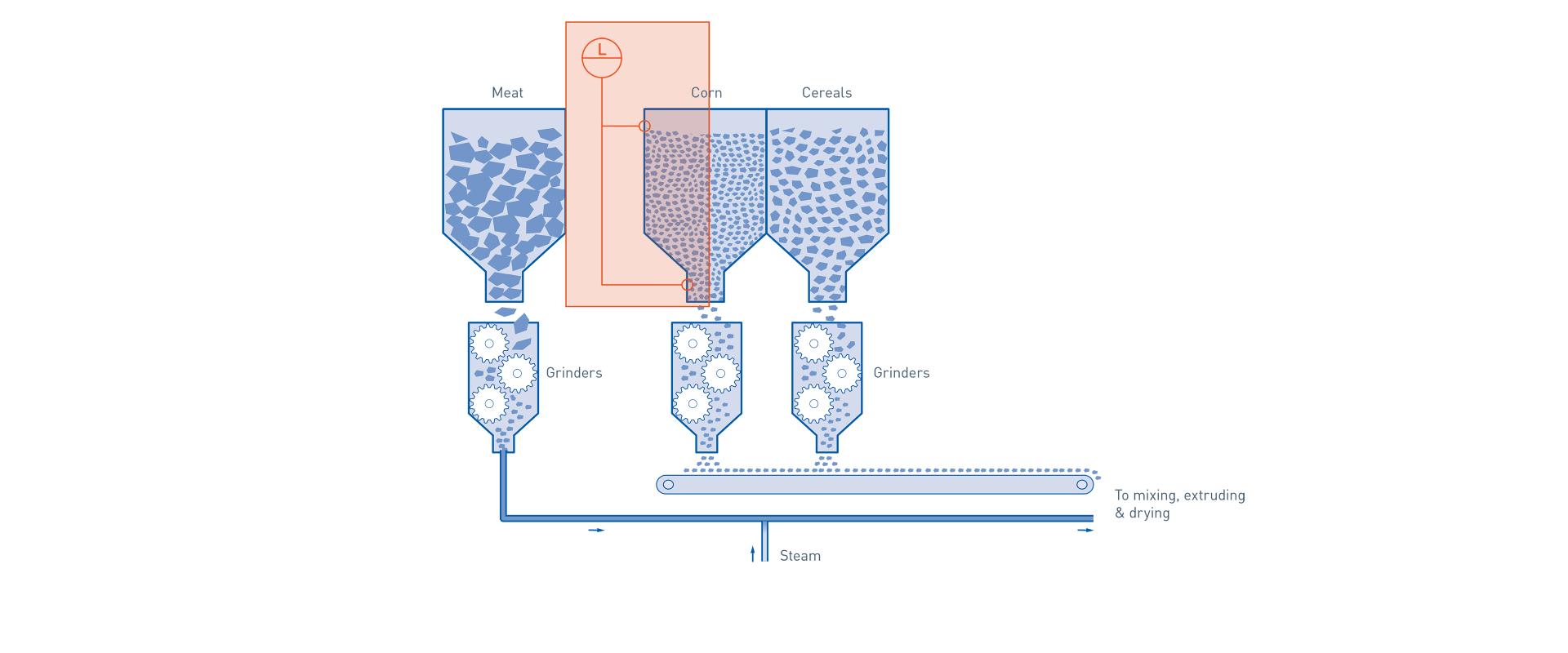
Requirements:
- Handling of dusty atmosphere
- High shear forces
Recommended products and solutions:
OPTISWITCH 6600
- Point level detection of solids, liquids and liquid-liquid interface
- Wide variety of hygienic process connections available
- -20…+200°C / -4…+392°F; -1…16 barg / -14.5…580 psig
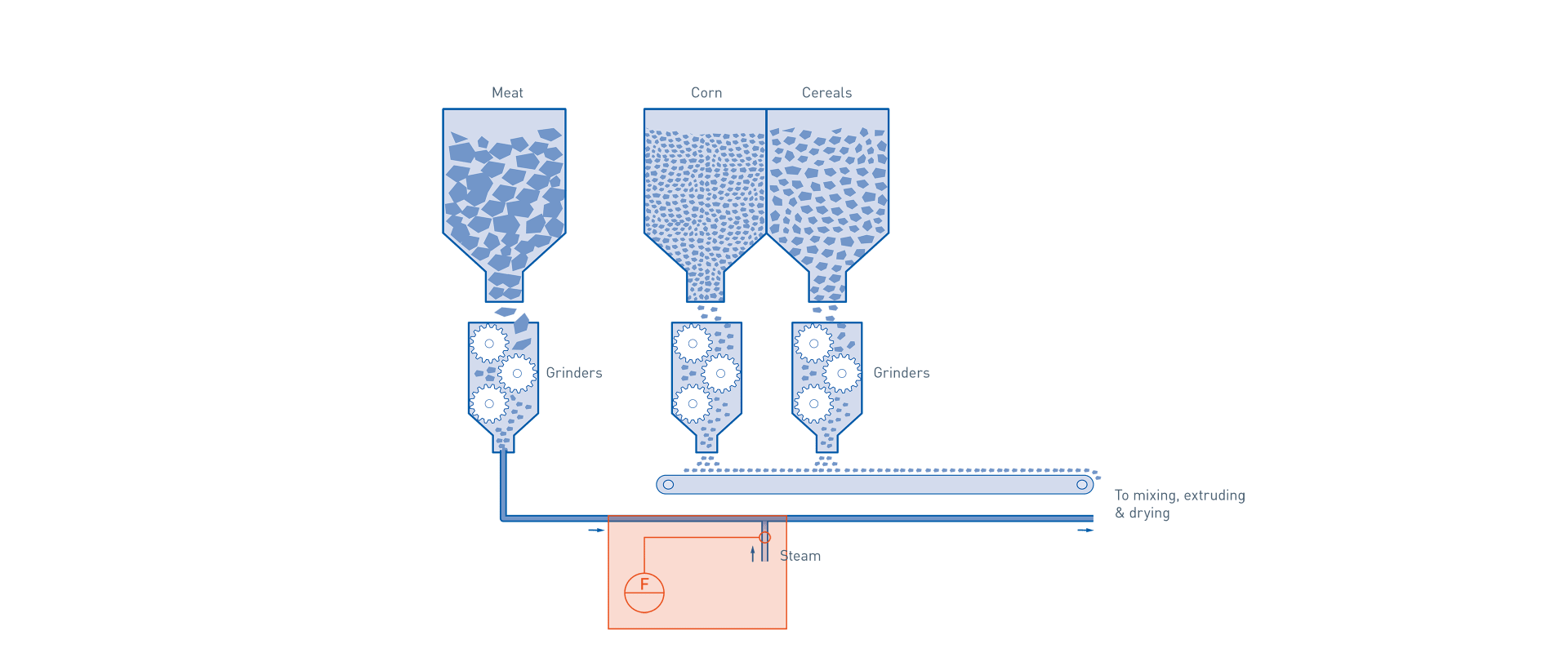
Requirements:
- Pressure/ temperature compensated
- Net heat measurement
Recommended products and solutions:
OPTISWIRL 4200
- For liquids, (wet) gases, saturated and superheated steam (+240°C / +464°F)
- Integrated P+T measurement: direct output of mass, nominal flow, energy, gross/net heat
- Flange: DN15…300 / ½…12"; wafer version: max. DN100 / 4"
- 2-wire, 4…20 mA, HART®, FF, Profibus-PA
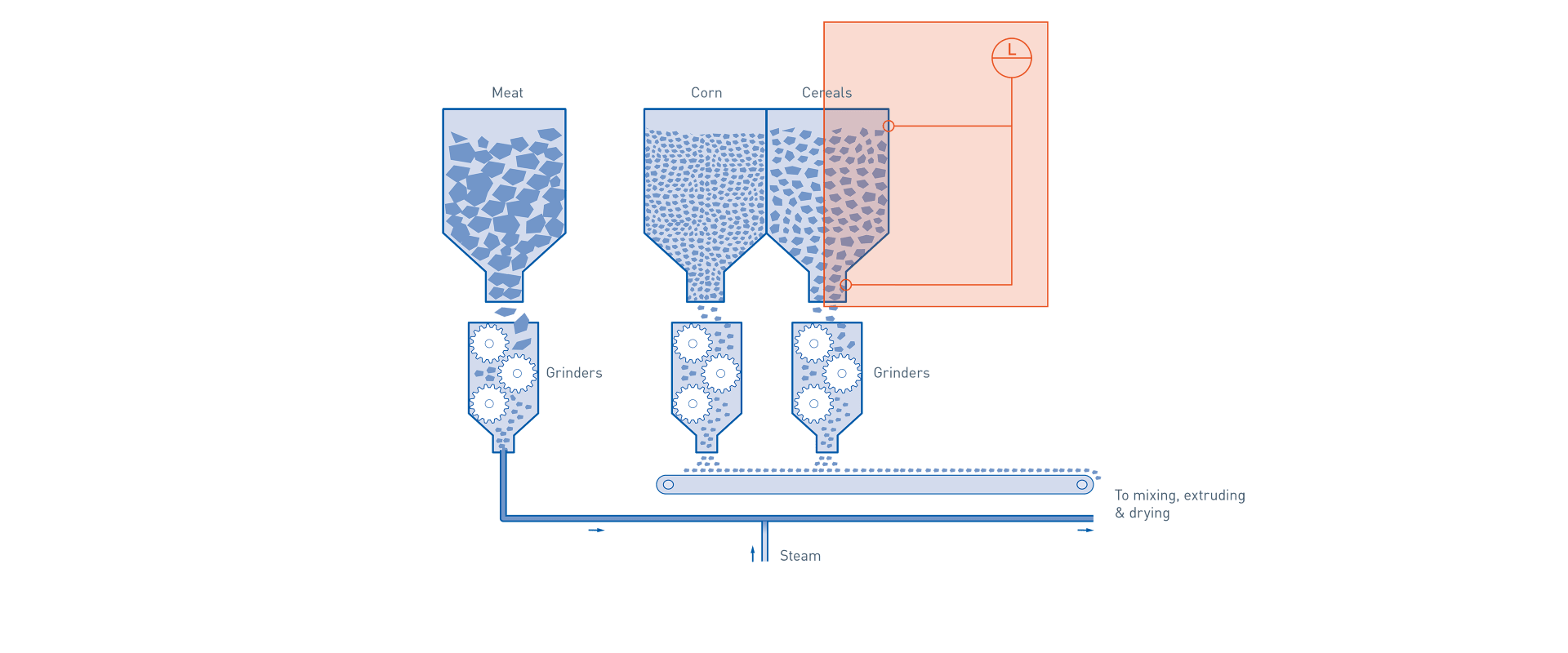
Requirements:
- Handling of dusty atmosphere
- High shear forces
Recommended products and solutions:
OPTISWITCH 6600
- Point level detection of solids, liquids and liquid-liquid interface
- Wide variety of hygienic process connections available
- -20…+200°C / -4…+392°F; -1…16 barg / -14.5…580 psig
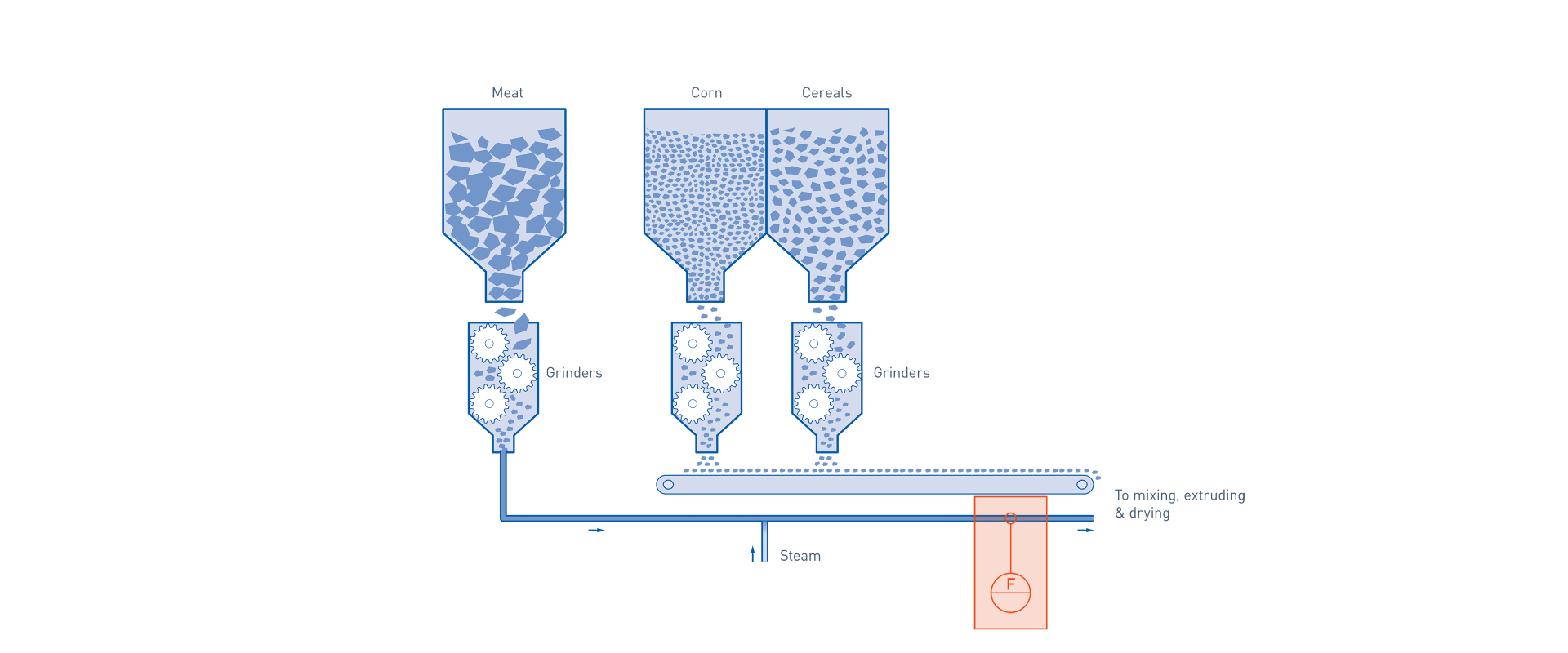
Requirements:
- Handling of very viscous media and high density
- Handling of air entrainment
Recommended products and solutions:
OPTIMASS 7400
- High accuracy (±0.1%), for viscous, aggressive or shear-sensitive media; maintains operation over a wide range of gas fractions and complex flow conditions (EGMTM)
- CT: OIML R117, MI-005; API; hygienic certifications
- Flange: DN10…100 / ½…4", max. PN100 / ASME Cl 600; others
- 3 x 4…20 mA, HART®7, Modbus, FF, Profibus-PA/DP, PROFINET, EtherNet/IP™, Bluetooth®
Requirements:
- Handling of very viscous media and high density
- Handling of air entrainment