Measuring level of coal on conveyors, silos and trains
Application Note | Metal & Mining
- Reliable level measurement on non-flat product surfaces
- Process automation from extraction to storage of coal
- Accurate level indication in dusty atmospheres
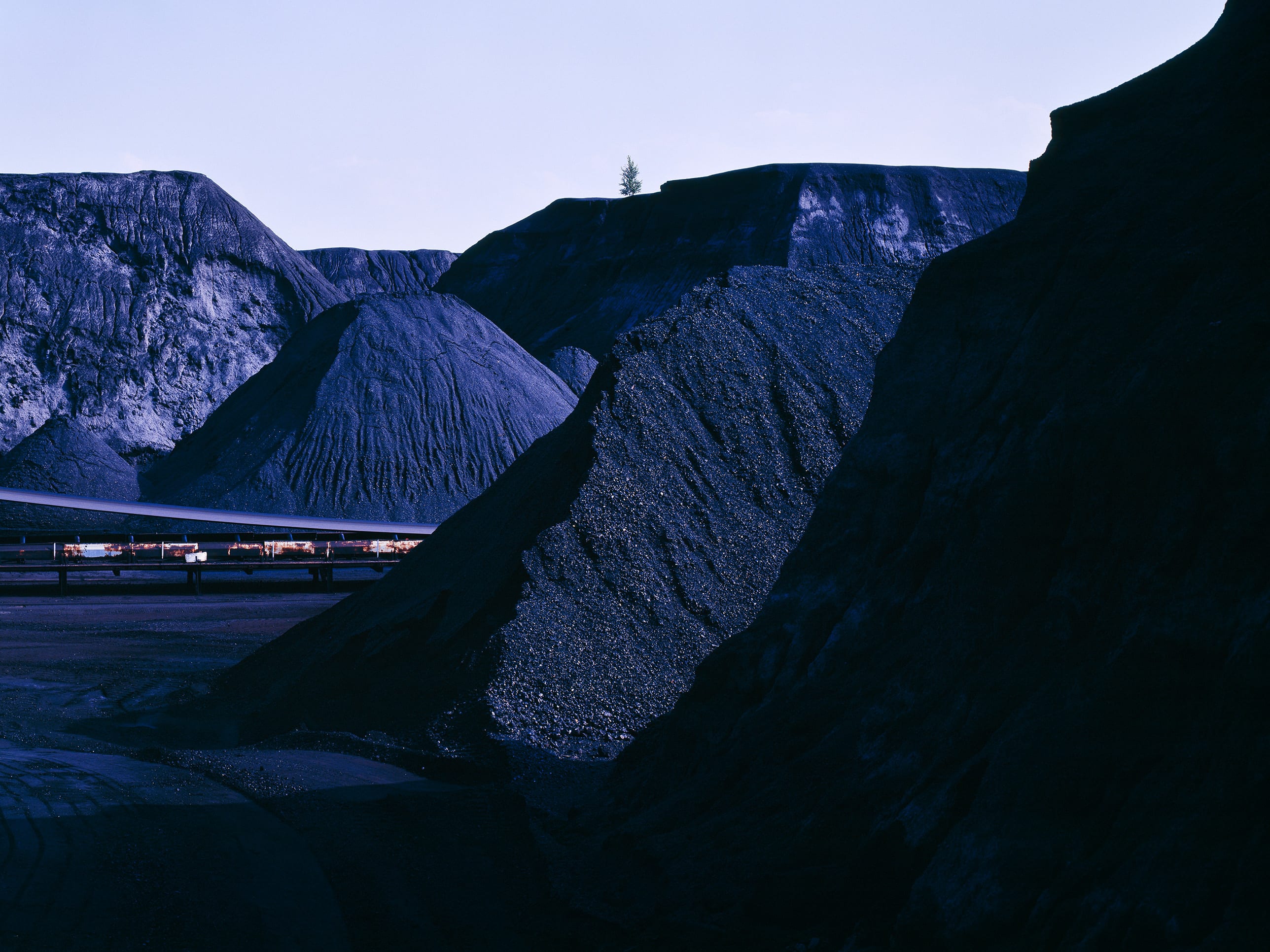
Background
The mining industry presents unique challenges due to dust, mud, impact, abrasion and build-up of material on sensors and plant machinery. Most coal mines are deep underground and require sub-surface mining, a method which currently accounts for about 60 % of world coal production. Our customer works a mine with 50 pits where coal is extracted from 800 meters underground.
Measurement requirements
The coal is carried up a lift and stocked in 2 buffer silos (18 m high). The two of them are half full with only one load from the lift. The level of the silo contents is regulated by a conveyor belt used for extracting the coal from below the storage silos and transporting it to a shuttle conveyor who leads the coal into the empty cells of 36 storage silos (20 m high). Conveyors running below these cells fill rail wagons that pass underneath these silos. The filling of the silos and wagons was monitored by pulse radars with large parabolic antennas and aiming kits. The pulse radar provides only a weak return signal when the pulse reflects off uneven product surfaces in a dusty environment. Under these circumstances, it was difficult to obtain accurate and reliable level data without antenna aiming kits and frequent cleaning of the antennas.
KROHNE Solution
KROHNE delivered 40 OPTIWAVE 6300 C contactless radar devices equipped with DN 80 Drop antennas made of plain PP and process connection 1”1/2 NPT where customer eventually screwed on his own flanges. The first 2 devices are installed above the buffer silos. They regulate the speed of the conveyor belt that extracts the coal from below the buffer silos. 36 devices on top of each storage silo control the equal filling of the storage cells and another 2 monitor the filling of the rail wagons.
Customer benefits
The challenging requirements of the mining industry were fully met using a robust technology offered at a competitive price. This solution allows the process to be automated from the extraction, storage to the shipment of coal. Furthermore, antenna aiming kits are no longer necessary for the reliable measurement of non fl at surfaces thanks to FMCW technology. The devices are easy to install and, being 2-wire transmitters, do not require as much wiring as 4-wire devices. PACTWARE allows remote commissioning by the customer himself. There is no need to cut large holes in the silo roof to install devices with huge parabolic antennas. The small antennas supplied with our devices are suffi cient for the application because the high-performance electronics amplifi es the return signal. Product build-up in dusty conditions is not an issue for drop antennas. Made of plain PP or PTFE, their shape and non-adhesive surface prevents a crust from forming, making purging systems obsolete. Using a drop antenna reduces installation and maintenance costs signifi cantly. This and the competitive price make the OPTIWAVE 6300 C a very cost-effective and attractive solution for the customer.