Custody transfer (CT) flow measurement for a natural gas fuel system
Application Note | Power Generation
- Flow metering solution for gas supply to load-flexible combined cycle gas turbine (CCGT) units
- Equipping fuel skids with calibrated metering sections and flow computers
- Maintenance-free operation and long-term stable, repeatable flow measurement using ultrasonic gas flowmeters
- Complete flow solution from one source: from engineering, instrumentation and flow computing to certification and commissioning
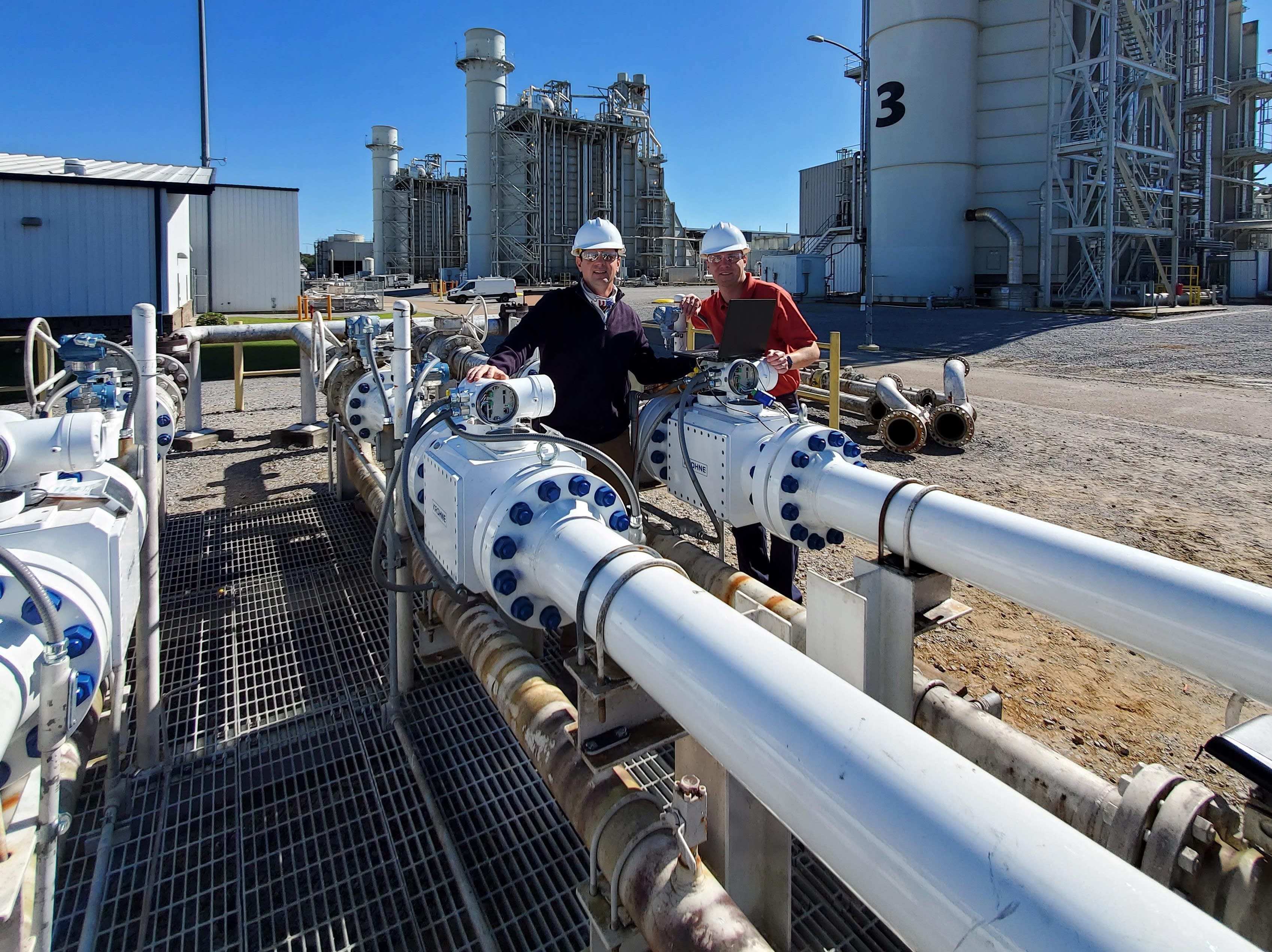
Background
Combined cycle gas turbine (CCGT) plants are clean, highly efficient and thanks to their load flexibility vital to stabilizing electricity grids fed with renewable energies. To provide their clients with reliable and stable electricity, a US electricity supplier operates an 800 MWel power station utilizing three CCGT units with heat recovery steam generators (HRSG). Each plant unit is equipped with an individual fuel gas pressure regulating and metering skid.
Measurement requirements
The main fuel gas consumers at CCGT plants are the gas turbines and the duct burners. The load rate of the plants can change quickly, resulting in a rapid change of fuel gas flow rate. For the feedlines to the three CCGT units, fuel systems perform a wide range of tasks, such as separation, fuel gas conditioning, pressure reduction (from 660 psi /45 bar to 64 psi / 4.4 bar) as well as custody transfer (CT) flow measurement and safety functions.
To measure fuel gas consumption, the customer had previously used turbine meters. Having been unsatisfied with the meter performance and maintenance requirements, the company started looking for a more reliable and accurate solution. The electricity supplier needed a complete natural gas flow solution as part of their fuel system to increase accuracy and plant availability as well as to reduce maintenance efforts. The solution was required to meet the local CT regulations according to AGA 9 as well as the regulations stipulated by the grid operator
KROHNE Solution
KROHNE supplied a metering solution consisting of three calibrated metering sections, pre-assembled and equipped with ALTOSONIC V12 ultrasonic gas flowmeters (UFM), pressure and temperature transmitters, certified SUMMIT 8800 flow computers and associated pipework. Engineering, related test documentation and final commissioning of the ready-to-operate solution has also been provided by KROHNE.
As a core element, three 8" ALTOSONIC V12 were installed for flow measurement of up to 2500 MSCFH of natural gas. The 12-chord ultrasonic CT gas flowmeter complies with multiple standards such as AGA 9, OIML R137, MI-002. It was the first ultrasonic flowmeter to be certified according to OIML R137 class 0.5 by a national metrology institute. Due to its unique ultrasonic path arrangement, the KROHNE flowmeter can compensate flow profile disturbances caused by restricted installation space much better than any other commercially available ultrasonic flowmeter in this category. There are also no moving or rotating parts and its sophisticated diagnostic options monitor the meter integrity and issues a warning in the event of fouling or condensate formation. The gas flowmeter features fast response and is able to cope with transient flow conditions without having any lifetime limitations.
Customer benefits
The electricity company operates their CCGT power plant units at high efficiencies and flexible loads. The KROHNE flow solution based on the ALTOSONIC V12 ultrasonic flowmeter supports in keeping efficiencies and plant uptime at high levels.
KROHNE provided the complete flow solution including engineering, instrumentation, pipe sections, flow computers, accessories, drawings, test documentation, certificates and commissioning. As a full solution provider, KROHNE can supply complete systems such as fuel systems for the supply of CCGT power plants, duct burners, air heaters or process heaters.